Sydney Contracting Engineers
Concrete Remedial Services
Concrete Remedial Services is a specialised field within the construction industry that focuses on rectifying and improving existing concrete issues. It encompasses everything from minor repairs to significant renovations, ensuring buildings are safe, functional, and compliant with current regulations. At the core of Concrete Remedial Services are key elements such as a thorough assessment of the structure, expertise in modern construction techniques, and a commitment to quality management. By addressing deficiencies, extending the lifespan of buildings, and preserving property value, Concrete Remedial Services play a crucial role in maintaining the integrity of residential and commercial properties.
What is Remedial Construction?
Remedial construction refers to the specialised field within the construction industry that focuses on rectifying existing problems in structures. This can include everything from minor repairs to major renovations, depending on the severity of the issues at hand.
Characteristics of Remedial Construction
- Assessment and Diagnosis: Before any remedial work can begin, a thorough assessment of the existing structure is necessary. This involves identifying the underlying problems and determining the best course of action, which is crucial for effective Concrete Remedial Services.
- Expertise and Specialisation: Concrete Remedial Services often require specific expertise. Professionals in this field must be skilled in various areas, including structural engineering, building codes, and modern construction techniques to ensure high-quality outcomes.
- Compliance with Regulations: All Concrete Remedial Services must adhere to local building codes and regulations. This ensures that any repairs or improvements made to the structure meet safety and quality standards.
- Project Management: Concrete Remedial Services projects often involve coordination among multiple trades and professionals. Effective project management is essential to ensure that all aspects of the work are completed efficiently and on schedule.
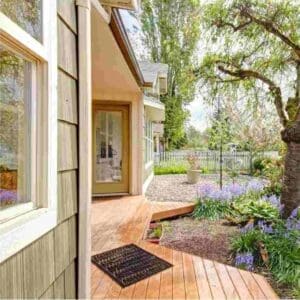
What Are Remedial Works For?
Remedial works serve several critical purposes within the realm of construction and housing. Here are some key functions:
1. Correcting Deficiencies
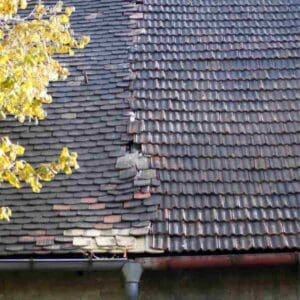
Remedial works aim to rectify any deficiencies in a building, whether they arise from design flaws, construction errors, or natural wear and tear over time.
2. Preserving Property Value
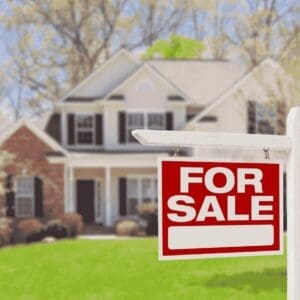
Regular remedial maintenance and repairs can significantly enhance a property’s value. A well-maintained home is more attractive to potential buyers and can command a higher market price.
3. Ensuring Safety and Compliance
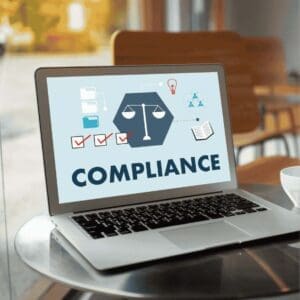
Remedial works help ensure that structures remain safe for occupancy. This includes addressing any safety hazards, complying with current building codes, and reducing liability for property owners.
4. Extending Lifespan of Structures
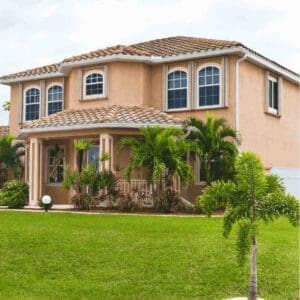
Through timely and effective remedial work, property owners can extend the lifespan of their buildings. Addressing issues early can prevent them from escalating into more severe problems that may necessitate costly replacements or extensive renovations.
Practical Tips for Homeowners Considering Remedial Work
If you’re a homeowner contemplating remedial work or renovation, it’s essential to approach the process with careful consideration and planning. Here are some practical tips to guide you through your remedial project:
1. Identify the Need for Remedial Work
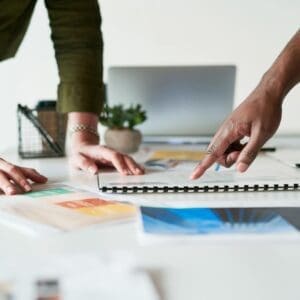
Start by assessing your property thoroughly. Look for signs of damage or deterioration, such as cracks in walls, water stains, or uneven floors. Keeping an eye on these issues can help you determine the necessity for remedial work and prioritise repairs effectively.
2. Consult with Professionals
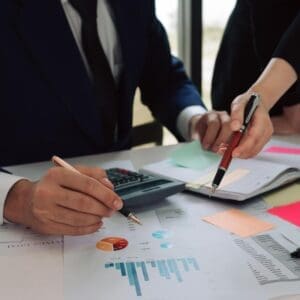
Before making any decisions, consult with qualified professionals. Engaging a structural engineer, architect, or experienced contractor can provide you with expert insights into the best approach for your specific situation. They can help identify underlying problems that may not be visible and recommend appropriate remedial solutions.
3. Obtain Multiple Quotes
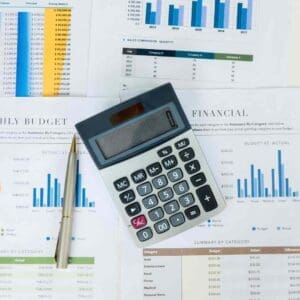
When hiring contractors for remedial work, it’s wise to obtain multiple quotes. This allows you to compare costs, services, and timelines. Be sure to check the credentials and references of each contractor to ensure you’re working with a reputable professional.
4. Understand the Scope of Work
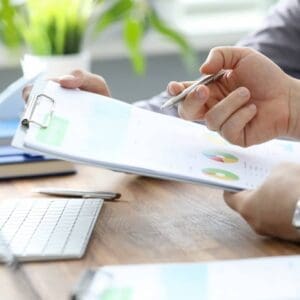
Clearly define the scope of the remedial work. This includes identifying what repairs or improvements need to be made and the expected outcomes. A detailed scope of work will help prevent misunderstandings and ensure that everyone involved is on the same page.
5. Plan for the Future
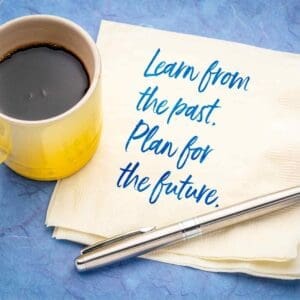
Consider how your needs may change in the future when planning your remedial work. For instance, if you anticipate expanding your family or working from home, think about how your renovations can accommodate those changes. Investing in flexible designs can save you from additional renovations down the line.
6. Focus on Quality Materials and Workmanship
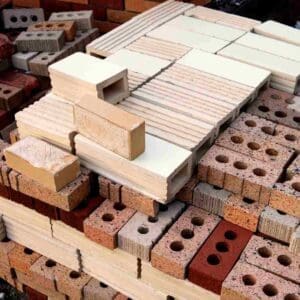
While it may be tempting to cut costs by opting for cheaper materials or contractors, this can lead to more significant expenses in the future. Investing in quality materials and skilled workmanship ensures that your remedial work stands the test of time, enhancing the safety and functionality of your home.
7. Stay Involved Throughout the Process
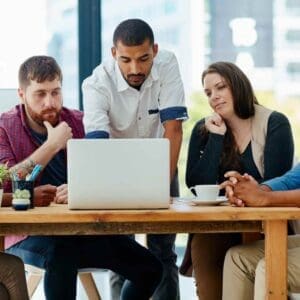
Maintain open communication with your contractor throughout the remedial work. Regular check-ins can help ensure that the project stays on track and allows you to address any concerns as they arise. Your involvement can lead to better outcomes and help avoid miscommunications.
Comprehensive Concrete Remediation Services by Sydney Contracting Engineers
At Sydney Contracting Engineers, we pride ourselves on providing comprehensive Concrete Remedial Services and renovation solutions for residential and commercial properties. As a fully licensed company holding the Design and Building Practitioners Registration, we are more than capable of delivering a wide range of Concrete Remedial Services. Whether it’s concrete cancer remediation, structural strengthening, or modern renovation techniques, our professional team is equipped to handle even the most complex Concrete Remedial Services projects.
What Does Concrete Remediation Mean in Construction?
Concrete Remedial Services involves the identification, assessment, and repair of concrete structures that have deteriorated due to various factors, such as environmental exposure, material defects, or structural stresses. This process ensures the longevity, safety, and aesthetic appeal of concrete elements in both residential and commercial properties through expert Concrete Remedial Services.
Concrete Cancer Remediation
One of the most common issues in concrete structures is concrete cancer (also known as reinforcement corrosion). It occurs when moisture enters the concrete and causes the steel reinforcement inside to rust. As the rust expands, it forces the surrounding concrete to crack, which can compromise the structural integrity of the building.
At Sydney Contracting Engineers, we offer concrete cancer remediation services that focus on treating the root cause of the issue. Our expert team identifies the affected areas, removes damaged sections, treats the steel reinforcement, and reinstalls high-quality concrete to prevent future corrosion. This process ensures the structural strength and longevity of your building.
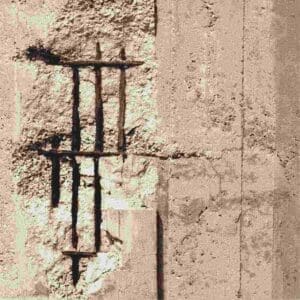
Concrete Spalling Remediation
Concrete spalling, often linked to concrete cancer, occurs when sections of the concrete surface begin to flake or chip away, usually due to exposure to moisture and environmental conditions. This damage can lead to safety hazards and aesthetic degradation, but more importantly, it signals underlying structural issues.
Our concrete spalling remediation services involve inspecting the area to determine the extent of the damage, removing the deteriorated concrete, and applying protective coatings to prevent further spalling. We are committed to delivering long-term solutions that ensure the durability of your structure.
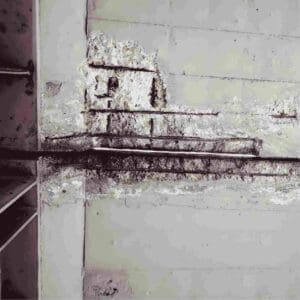
Concrete and Asphalt Resurfacing
Over time, surfaces like concrete and asphalt can become worn, cracked, or damaged due to heavy use, weather conditions, or material degradation. Resurfacing these areas not only enhances the appearance of the surface but also strengthens it, preventing further deterioration and improving safety.
At Sydney Contracting Engineers, we specialise in concrete and asphalt resurfacing for driveways, car parks, footpaths, and industrial floors. We use durable materials and advanced techniques to deliver smooth, long-lasting finishes that can withstand high traffic and harsh environmental conditions. Our resurfacing solutions are designed to be both cost-effective and durable, providing excellent value for our clients.
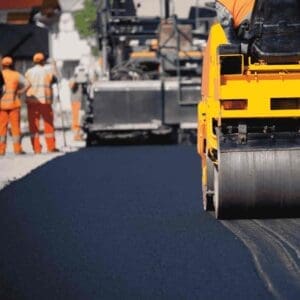
Why Choose Sydney Contracting Engineers for Your Concrete Remediation?
At Sydney Contracting Engineers, we provide a comprehensive range of Concrete Remedial Services, supported by our Design and Building Practitioners Registration and industry certifications. Our skilled team is prepared to manage projects of all sizes and complexities, from minor residential repairs to extensive commercial Concrete Remedial Services.
Key Benefits of Our Services:
- Expert Team: Our engineers and technicians are fully licensed and trained to perform a wide variety of Concrete Remedial Services, ensuring the highest standards of quality and safety.
- Tailored Solutions: We customise our strategies to address the specific requirements of your project, whether it involves a residential or commercial property requiring Concrete Remedial Services.
- Long-Term Solutions: We focus on delivering durable solutions that tackle the root causes of concrete issues, helping to prevent costly future repairs through expert Concrete Remedial Services.
- Sustainability: We strive to use eco-friendly materials and practices whenever possible, ensuring our Concrete Remedial Services are environmentally responsible.
- Regulatory Compliance: Our team guarantees that all Concrete Remedial Services work adheres to Australian building codes and regulations, providing you with peace of mind.
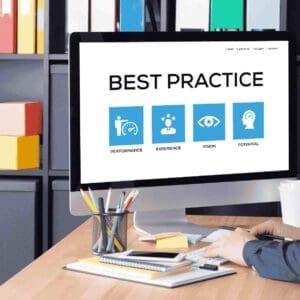
Contact Us Today
At Sydney Contracting Engineers, we have the expertise and commitment to deliver exceptional Concrete Remedial Services and renovation solutions. From concrete cancer remediation and structural strengthening to concrete resurfacing, we handle it all with precision and professionalism. Our Concrete Remedial Services are tailored to address a variety of issues, ensuring your property is maintained, restored, and improved. Contact us today to discuss your project and learn how we can help you with our expert Concrete Remedial Services.
FAQ
1. What is the relationship between remedial works and concrete issues like cancer, cracks, or spalling?
Remedial work is crucial for addressing issues like concrete cancer, cracks, and spalling. This type of remedial intervention involves removing the affected concrete to expose any underlying problems. Once the damaged concrete is removed, the steel reinforcement must be treated to prevent further corrosion. After this treatment, the area is repaired with new concrete, ensuring that the structural strength is restored effectively. The overall goal of remedial work is to enhance the durability and safety of the structure, making it imperative to implement comprehensive remedial solutions whenever concrete issues arise. Proper remedial practices not only fix existing problems but also help prevent future deterioration, underscoring the importance of thorough remedial assessments and actions.
2. How can I identify the need for remedial works due to concrete cancer or cracks?
Identifying the need for remedial works is essential when observing signs of concrete issues, such as cracking or crumbling concrete. These signs often indicate that remedial action is necessary to restore the structural integrity of the material. Rust stains emerging from the concrete or cement render are another clear indication that remedial measures should be considered, as they suggest underlying corrosion of the reinforcement. Regular monitoring for these common signs can help determine when remedial work is required, allowing for timely interventions. By addressing these issues through appropriate remedial solutions, you can prevent further deterioration and maintain the durability of the structure. Ultimately, being vigilant about signs of cracking, crumbling, and rust will guide you in recognizing when remedial actions are critical for preserving concrete integrity.
3. What are the common causes of concrete cancer, and how can remedial works help?
Concrete cancer is primarily caused by the corrosion of steel reinforcement due to factors like moisture infiltration, chloride exposure, and poor-quality materials. Remedial works are essential in addressing these issues effectively. The first step in the remedial process is a thorough assessment to determine the extent of damage and underlying causes. Following this, remedial actions involve removing the damaged concrete to expose the reinforcement, which is then treated with rust inhibitors to prevent further corrosion. New, high-quality concrete is used to fill the void, and additional remedial measures, such as applying protective sealants, help mitigate future risks. Improved drainage solutions are also part of the remedial strategy, reducing water accumulation and minimising the chance of concrete cancer reoccurring. By implementing these comprehensive remedial works, the structural integrity of the concrete can be restored and maintained over time.
4. What are the typical remedial solutions for addressing concrete cancer?
Remedial actions are essential in addressing various structural issues, particularly in concrete structures. When assessing the need for remedial work, it is crucial to identify signs of damage, such as cracks, spalling, or discoloration. These indicators often necessitate immediate remedial interventions to restore integrity and safety. Typical remedial solutions include removing affected areas, treating any corrosion, and applying new materials that enhance durability. Additionally, implementing drainage improvements and protective coatings are key components of a comprehensive remedial strategy. Regular monitoring ensures that any future issues are caught early, allowing for timely remedial actions. Overall, a proactive approach to remedial maintenance can significantly extend the lifespan of concrete structures and prevent costly repairs down the line.
5. What steps are involved in the remedial process for repairing spalling concrete?
The remedial process for repairing spalling concrete involves several critical steps that ensure effective restoration. First, the damaged concrete must be removed, which is a vital part of the remedial approach to eliminate any deteriorated material. Next, the surface is thoroughly prepared to create a solid foundation for the repair. This preparation is essential in the overall remedial strategy to ensure proper adhesion of the new material. Finally, applying a suitable repair system completes the remedial process, providing strength and durability to the repaired area. By focusing on these three key steps—removing the damaged concrete, preparing the surface, and applying a repair system—remedial works can effectively restore the integrity of the concrete and prevent further deterioration. Regular monitoring after the remedial actions are implemented is also crucial to ensure the long-term success of the repairs.
6. How do remedial works differ when addressing concrete cracks compared to concrete spalling?
Remedial works differ significantly when addressing concrete cracks compared to concrete spalling, highlighting the need for tailored remedial approaches. For cracks, the remedial process typically begins with assessing the type and severity, followed by remedial methods such as crack injection or routing and sealing to ensure effective repair. In contrast, remedial actions for spalling require a more extensive approach, often involving the removal of damaged concrete to expose and treat the underlying reinforcement. This remedial work is crucial for preventing further deterioration. Additionally, after repairing spalled areas, applying protective coatings serves as a vital part of the remedial strategy. Overall, recognising the specific issues at hand allows for effective remedial solutions that enhance the durability and safety of concrete structures. By implementing the appropriate remedial measures, both cracks and spalling can be effectively addressed, ensuring the longevity of the concrete.
7. How can I assess the severity of concrete cracks to determine if remedial works are necessary?
Assessing the severity of concrete cracks is crucial in determining the need for remedial works. If the cracks are only hairline or small in size, they are often considered normal and typically do not pose significant structural issues, thus requiring minimal or no remedial action. However, it is important to monitor these small cracks as part of a remedial maintenance plan, ensuring they do not develop into larger problems over time. If any hairline cracks start to widen or show signs of movement, this may indicate a shift in structural integrity that necessitates more extensive remedial measures. Therefore, a proactive approach to monitoring even minor cracks can help identify when remedial works become necessary, ensuring the overall safety and longevity of the concrete structure. By understanding the distinction between normal and problematic cracks, you can better decide when remedial interventions are warranted.
8. How does weather affect the effectiveness of remedial works for concrete damage?
Weather significantly affects the effectiveness of remedial works for concrete damage, particularly in high temperatures. When temperatures are elevated, concrete can hydrate too quickly, which compromises its overall strength and longevity. This rapid hydration is a critical factor in the remedial process, as it can lead to surface cracking and reduced durability of the repaired areas. To ensure successful remedial outcomes, it is essential to monitor weather conditions closely and plan remedial actions accordingly. Implementing cooling techniques, such as wetting the surface or using retarders, can help manage the hydration process during hot weather. By understanding the impact of temperature on concrete hydration, remedial works can be optimised to achieve the best possible results, preserving the integrity and lifespan of the structure. Ultimately, careful attention to weather conditions is a vital aspect of any effective remedial strategy.
9. What preventive measures can be taken during remedial works to avoid future issues with concrete cancer or cracks?
Preventive measures during remedial works are crucial for avoiding future issues with concrete cancer or cracks. First, using high-quality materials ensures durability and resistance to environmental factors. Proper mix design minimises permeability, reducing moisture infiltration. Maintaining adequate cover over steel reinforcement protects it from corrosion. Implementing effective drainage solutions prevents water accumulation around the structure, while applying protective coatings creates a barrier against moisture. Establishing a routine maintenance program allows for early detection and addressing of minor issues. Controlled curing techniques ensure optimal hydration and strength development, especially in extreme weather conditions. Monitoring for movement with crack detection devices enables timely remedial action, and proper joint design accommodates expansion and contraction, preventing cracking. By incorporating these preventive measures during remedial works, the risk of future concrete cancer and cracks can be significantly reduced, ensuring the long-term integrity of the structure.
10. Are there specific materials used in remedial works for repairing concrete cancer or spalling?
In remedial works for repairing concrete cancer or spalling, specific materials play a crucial role in ensuring effective restoration. Remedial processes often utilise epoxy resins for bonding and sealing cracks, as they provide strong reinforcement. Additionally, polyurethane sealants are commonly used in remedial applications for their flexibility and moisture resistance, making them ideal for sealing joints. Specialised polymer-modified repair mortars are essential in the remedial approach to patch spalled areas, offering enhanced adhesion and durability. Incorporating corrosion inhibitors into remedial mortars helps protect steel reinforcement from further damage. Cementitious coatings serve as a vital part of the remedial strategy, enhancing surface durability and resisting moisture ingress. Self-levelling compounds are also employed in floor repairs to address spalling effectively. By using bonding agents to improve adhesion and specialised grouts for void filling, the overall effectiveness of the remedial works is maximised. Selecting the right materials is key to successful remedial interventions, ultimately extending the lifespan of concrete structures impacted by cancer or spalling.
11. What is the expected timeframe for completing remedial works on a property with concrete cancer or severe cracking?
The expected timeframe for completing remedial works on a property with concrete cancer or severe cracking can vary significantly based on several factors. The extent of the damage is crucial. Minor remedial repairs may take a few days, while extensive issues could extend the timeframe to several weeks or even months. The type of remedial works required, such as surface preparation, concrete removal, and reapplication, also influences the timeline. Additionally, the curing time for various repair materials is a vital consideration, as some may need several days to cure properly before further remedial actions can be taken. Weather conditions can further affect the effectiveness of remedial works, with high humidity or extreme temperatures potentially causing delays. Access to the site and logistics regarding material transport can also play a role in the overall timeframe. Finally, any necessary permits or inspections may add additional time to the remedial process. On average, small to moderate remedial works may take between one to four weeks, while more extensive repairs could require several weeks to a few months, highlighting the importance of consulting with professionals for accurate estimates on remedial timelines.
12. How do I document the condition of my concrete before and after remedial works?
Documenting the condition of concrete before and after remedial works is essential for assessing the effectiveness of repairs and maintaining a clear record. Prior to any remedial actions, conduct a thorough visual inspection to identify visible damage, such as cracks and spalling, and take detailed photographs to capture the extent of the issues. Writing detailed descriptions, including measurements of cracks and environmental conditions, is crucial for effective documentation. During the remedial process, it is important to take progress photos and maintain a log of all activities, detailing specific remedial actions taken and materials used. After the remedial works are completed, conduct a final inspection and take additional photographs to compare against the pre-repair documentation. Performing any relevant performance tests will further validate the effectiveness of the remedial repairs. Compiling all documentation, including photos, reports, and logs, into a comprehensive file ensures that all aspects of the remedial process are recorded. This thorough documentation will be invaluable for future monitoring and maintenance of the concrete, helping to address any ongoing issues effectively.
13. Can ongoing maintenance help prevent the need for future remedial works on concrete surfaces?
Ongoing maintenance plays a crucial role in preventing the need for future remedial works on concrete surfaces. By conducting regular inspections, property owners can detect minor issues such as cracks or spalling early, allowing for timely remedial repairs before they escalate into larger problems. Routine cleaning is essential, as it removes debris and chemicals that can contribute to deterioration, thereby reducing the need for extensive remedial actions. Applying protective sealants periodically serves as a preventive measure, helping to shield the concrete from moisture and environmental elements that could lead to damage. Additionally, ensuring proper drainage prevents water accumulation, a common cause of concrete cancer, and helps avoid costly remedial interventions. By promptly addressing minor imperfections, the risk of requiring more significant remedial works in the future is minimised. Monitoring environmental conditions further aids in planning maintenance and remedial actions effectively. Overall, a proactive maintenance plan significantly extends the lifespan of concrete surfaces, reducing the likelihood of future remedial works and ensuring long-term durability and safety.
Thank you for your visit, and welcome to the construction home