Blog Post -Inflation is a critical economic factor that can significantly impact industries across the globe, including the construction sector. For those working within the construction industry, inflation presents both opportunities and challenges. This article explores the influence of inflation on the construction industry, focusing on its impact on material costs, supply chains, and construction cost estimation. By understanding how inflation affects these key areas, industry professionals can better navigate the current economic landscape.
What is Inflation and How Does It Impact the Construction Industry?
Inflation refers to the rate at which the general level of prices for goods and services rises, causing a decrease in purchasing power. In the context of the construction industry, inflation primarily affects material costs, labour costs, and overall project budgets. As the cost of raw materials and transportation rises, construction firms face higher expenditure, which can lead to increased project costs, delayed timelines, and potential contract renegotiations.
For example, construction material costs like timber, steel, and concrete have surged during periods of high inflation, straining budgets and making cost management more difficult. Moreover, inflation can result in a rise in interest rates, which may affect financing options for construction projects, further complicating the financial side of operations.
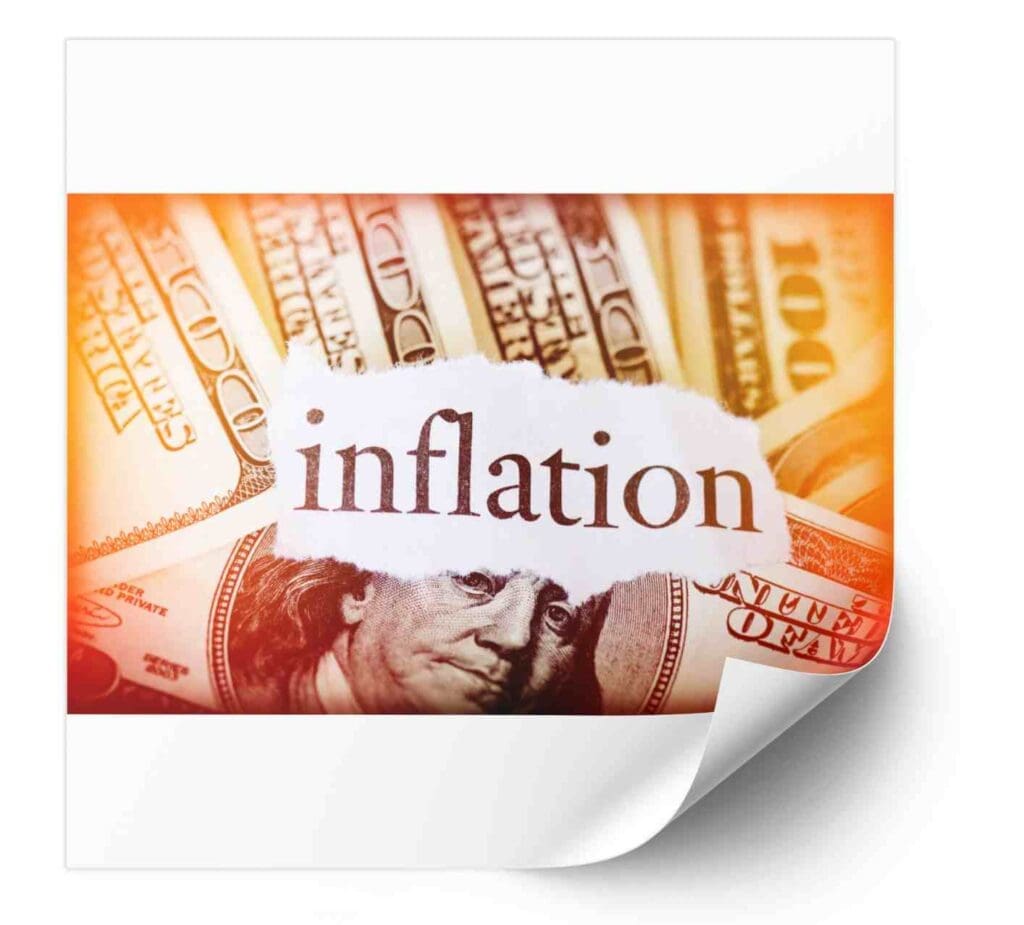
Inflation’s Influence on the Supply Chain in Construction
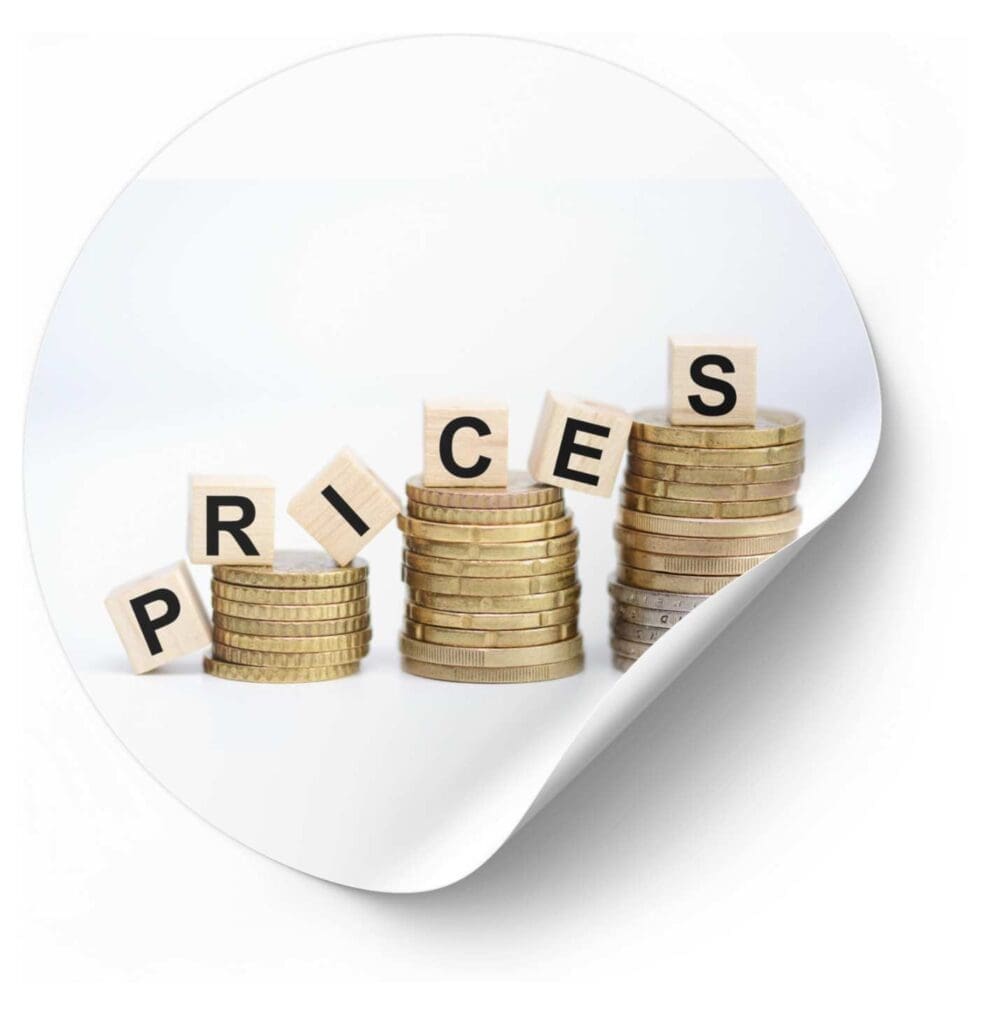
The construction industry relies on a complex supply chain, involving the sourcing of raw materials, equipment, and labour. As inflation drives up the costs of these goods and services, it leads to several challenges. For example, if fuel prices rise, the cost of transporting materials to construction sites increases. Additionally, global supply chains are often disrupted due to inflationary pressures, which can lead to delays in receiving essential materials.
Inflation in the construction supply chain may cause a shortage of key materials. When demand outpaces supply due to higher prices, projects can experience delays, forcing contractors to find alternative suppliers or materials. This can further escalate project costs as contractors face price volatility.
In addition to raw materials, the availability of skilled labour is also affected by inflation. As wages increase to keep up with the cost of living, construction firms may need to adjust their budgets to account for higher labour costs. This can impact project timelines and ultimately affect the overall cost of construction projects.
Key Areas Affected by Inflation in the Supply Chain
Inflation affects various aspects of the construction supply chain, including:
Raw Materials: Materials such as steel, timber, cement, and glass see price increases when inflation hits, directly affecting the overall cost of construction. This also impacts the procurement process, as contractors must adapt to fluctuating prices.
Labour Costs: To attract skilled workers, wages must rise to keep up with the cost of living. This not only affects current projects but also complicates labour forecasting for future projects.
Transportation: Inflation can drive up fuel prices, which in turn increases the cost of transporting materials to construction sites. This can cause delays and escalate transportation costs.
Energy Prices: The cost of energy, such as electricity and gas, can also increase during periods of inflation. Construction projects that rely on energy-intensive processes may face higher operational costs as a result.
These factors underscore the need for construction professionals to develop strategies to cope with inflation-related disruptions and costs.
Supply Chain Challenges in Construction
The construction industry’s supply chain faces several challenges, and inflation exacerbates these difficulties. Some of the most common challenges include:
1. Material Shortages and Delays
As inflation leads to higher demand for raw materials, construction firms may find themselves struggling with shortages. If suppliers cannot meet the demand or if production slows, projects can experience delays. This can disrupt construction schedules, leading to extended project timelines and increased costs.
In addition to shortages, inflation can also lead to price fluctuations that make it difficult for contractors to lock in material costs. This uncertainty can complicate project budgeting and risk management.
2. Increased Lead Times for Materials
When inflation affects global supply chains, it can result in longer lead times for materials. Construction firms often rely on materials that are sourced globally, and when inflation increases, delays in transportation, customs clearance, and shipping can occur. Longer lead times can prevent construction companies from meeting their project deadlines.
3. Fluctuating Fuel Prices
Fuel prices are a significant contributor to the rising costs in the construction supply chain. Construction vehicles, machinery, and transport trucks rely on fuel to move materials to construction sites. When fuel prices increase due to inflation, transportation costs for all goods in the supply chain are impacted, leading to higher overall project costs.
4. Reduced Supplier Stability
Suppliers may struggle to manage their own rising costs during times of inflation, potentially leading to financial instability. If a supplier faces difficulty in maintaining operations due to rising costs, they may be forced to close, leading to a breakdown in the supply chain. This can disrupt construction schedules and force contractors to find alternative suppliers, which may come with additional costs.
These challenges highlight the importance of having reliable suppliers and well-established contingency plans to mitigate supply chain disruptions during inflationary periods.
Managing Supply Chain Risk During Inflation
To manage supply chain risks during inflation, construction professionals should:
Diversify Suppliers: Working with multiple suppliers can reduce dependency on a single source and help ensure more reliable delivery schedules.
Negotiate Long-Term Contracts: Negotiating fixed-price contracts for materials can help protect against price fluctuations and ensure cost predictability.
Monitor Market Trends: Keeping a close eye on the market and inflationary trends can help construction firms anticipate price changes and plan accordingly.
Understanding these challenges and taking proactive steps can help mitigate the impact of inflation on the construction industry’s supply chain.
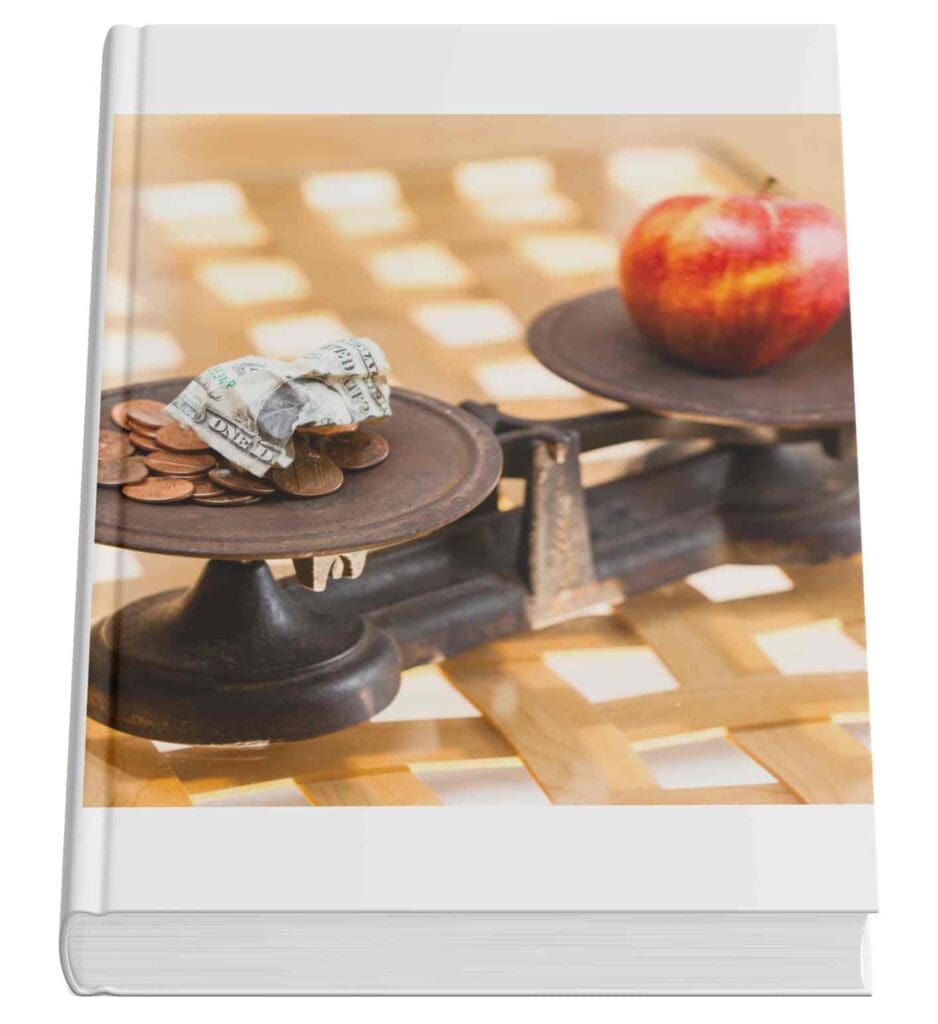
Impact of Inflation on Material Costs
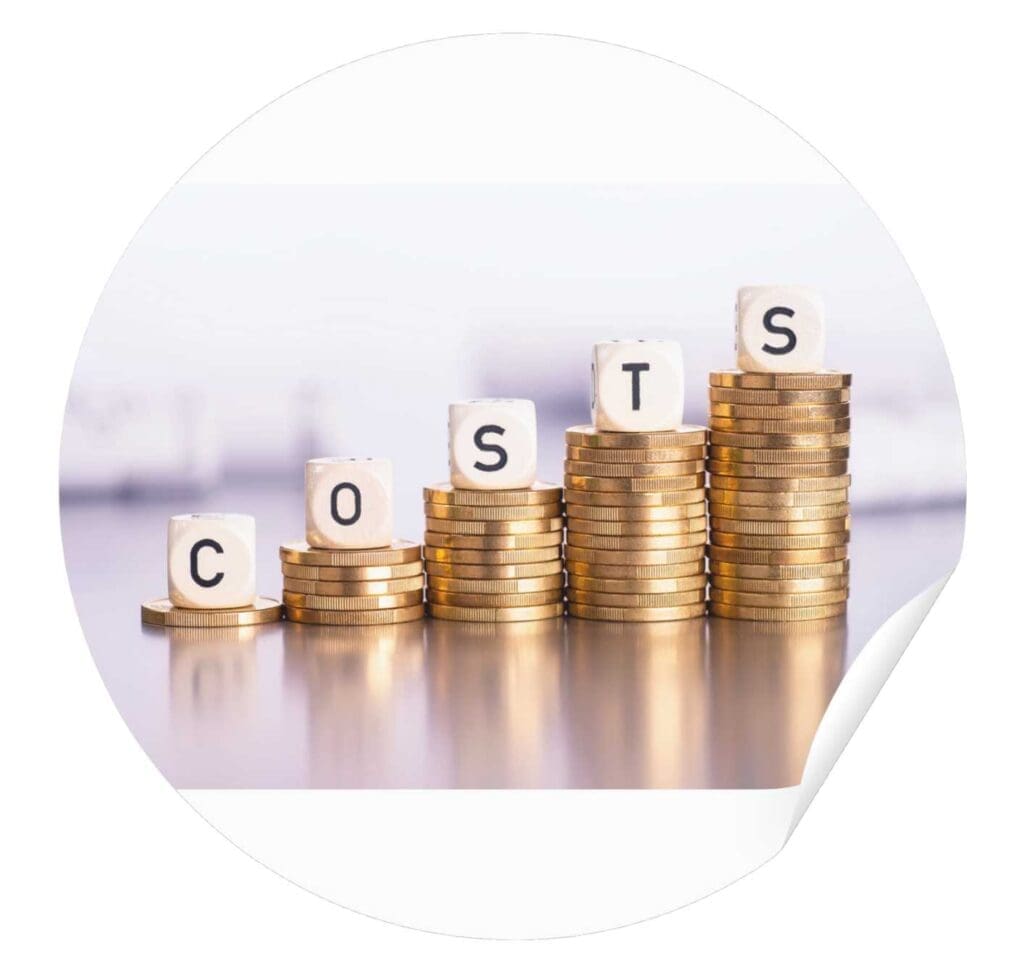
The cost of construction materials is one of the most visible impacts of inflation in the industry. Inflation has historically led to spikes in the price of materials, causing direct consequences on construction budgets. These materials are essential for most projects, and when their costs rise, contractors are forced to adapt to maintain profitability.
Rising Prices for Key Construction Materials
Some of the most significant material cost increases during inflationary periods include:
Steel: Steel prices tend to surge during inflation as it is heavily reliant on global supply chains and raw materials. The rising cost of steel directly impacts the cost of constructing infrastructure, buildings, and roads.
Timber: Timber is another material that experiences price volatility during inflation. Shortages caused by rising demand can result in inflated prices, leading to higher construction costs.
Concrete: Concrete, a primary material for most construction projects, is also affected by inflation. Rising energy costs, especially the cost of electricity for cement production, can lead to increased concrete prices.
Plumbing and Electrical Supplies: As inflation impacts commodity prices, it also affects the cost of plumbing and electrical materials. These are integral components of most building projects, making price increases particularly impactful.
For construction companies, higher material costs are often passed onto clients, but this can sometimes lead to disputes or delays if budgets are not updated to reflect the increased expenses. Moreover, these cost increases can affect small contractors who have limited margins and less flexibility in negotiating prices.
Strategies for Managing Material Cost Increases
To manage the rising costs of materials, construction companies can:
Bulk Purchasing: Buying materials in bulk before prices rise can help secure lower rates and reduce the impact of inflation.
Substitution of Materials: In some cases, alternative materials may be used to offset cost increases. For example, replacing steel with aluminium or exploring alternative concrete mixes may provide cost savings.
Lean Construction: Implementing lean construction practices can help reduce waste and ensure that material usage is optimised, thereby minimising unnecessary costs.
As inflation drives up material costs, these strategies can help mitigate some of the financial pressure on construction firms.
This concludes the first part of the article. Stay tuned for the next section, where we will delve into challenges in construction cost estimation, strategies for managing these challenges, and the long-term effects of inflation on the industry.
Challenges in Construction Cost Estimation
Accurate construction cost estimation is crucial to the success of any project, but inflation has introduced several challenges that complicate this process. The fluctuating costs of materials, labour, and operational overheads make it difficult for construction professionals to predict project expenses with certainty. In this section, we will examine how inflation affects cost estimation, the key factors that impact cost accuracy, and strategies that can be employed to improve cost forecasting in an inflationary environment.
The Influence of Inflation on Cost Estimation
Inflation has a direct impact on construction cost estimation, as it drives up the cost of materials, labour, and fuel. As prices increase, construction firms must adjust their estimates to accommodate these rising costs. However, inflation is unpredictable, and its rate of increase can vary, making it difficult to accurately forecast costs for the entire project duration.
For instance, if inflation causes an unexpected rise in material prices during the project, contractors may find themselves underestimating costs. Similarly, as wages increase due to inflation, contractors must also revise labour costs accordingly. Inaccurate estimates can lead to budget overruns, project delays, and ultimately, financial strain for construction firms.
The Role of Labour Costs in Construction Cost Estimation
Labour costs represent a significant portion of any construction budget, and inflation directly impacts these costs. As the cost of living rises, so do wages, making it essential for construction professionals to factor in these increases when estimating labour expenses.
As inflation puts pressure on wages, construction companies may need to offer higher salaries to attract and retain skilled workers. This increase in wages, while necessary, drives up the overall project cost. Additionally, fringe benefits, insurance premiums, and other worker-related expenses can also increase, further complicating the estimation process.
Inflation also affects labour productivity. When wages rise, workers may become more demanding in terms of benefits and compensation, leading to potential disruptions in productivity. Cost estimators must account for these potential shifts in both labour cost and productivity when creating budgets for construction projects.
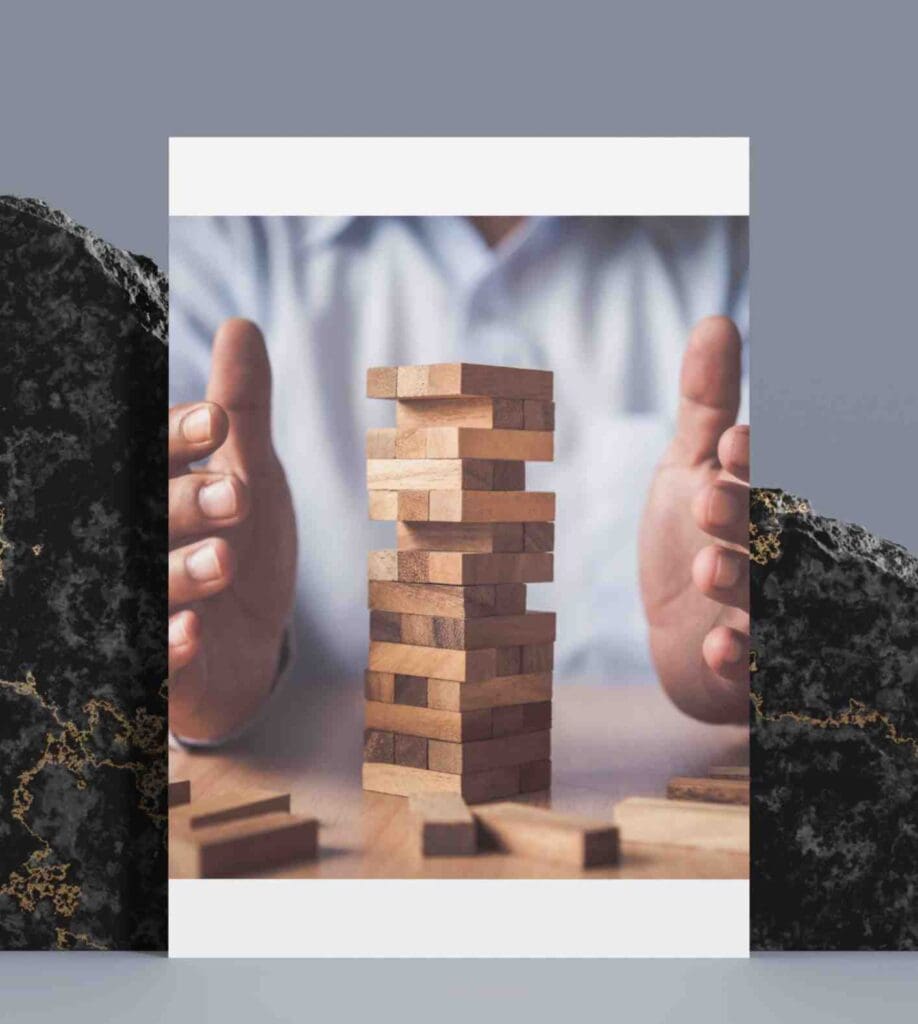
Fuel Prices and Their Impact on Estimation Accuracy
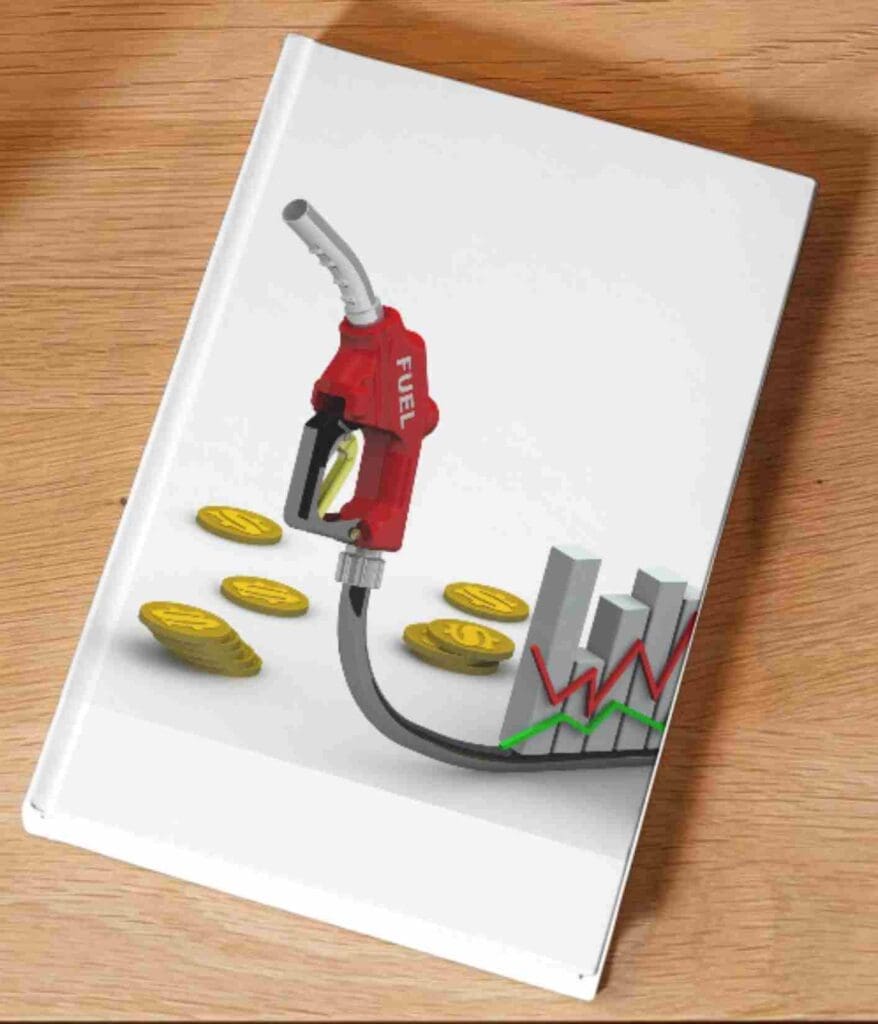
Fuel prices are another key factor in construction cost estimation, especially in projects that require heavy machinery, transportation, and equipment. When inflation drives up fuel prices, operational costs for construction companies can escalate rapidly. This not only affects fuel costs for machinery and transportation but also influences the cost of moving materials to and from the site.
The volatility of fuel prices makes it challenging to create accurate cost estimates for construction projects. If fuel prices rise unexpectedly during a project, the cost of transporting materials, equipment, and labour to the site may exceed initial estimates. This could lead to cost overruns unless fuel price increases are anticipated and factored into the budget.
Material Price Volatility and Inflation
Material costs are one of the most significant variables in construction cost estimation. Inflation can cause the price of key construction materials such as steel, timber, and concrete to fluctuate dramatically, which poses a challenge for accurate forecasting.
When inflation affects material prices, contractors may find themselves unable to lock in the cost of materials for the duration of the project. As a result, if prices rise midway through construction, the overall cost of the project could exceed the original budget. This material price volatility underscores the importance of considering inflation when estimating construction costs and provides the rationale for including contingency budgets in project estimates.
The Impact of Exchange Rates on Imported Materials
For construction projects that rely on imported materials, fluctuations in exchange rates can complicate cost estimation. The rising value of foreign currencies, driven by inflationary pressures in other countries, can increase the cost of imported goods. Similarly, a weakening local currency can lead to higher prices for materials sourced internationally.
In such cases, inflationary pressures may make imported materials significantly more expensive, which must be taken into account in cost estimates. When exchange rates fluctuate, construction firms may face higher-than-expected costs for items such as machinery, steel, and specialty materials, which are often sourced from overseas.
Estimating Costs Amidst Inflationary Pressures
Given the many factors that inflation affects in construction cost estimation, it’s crucial to adopt proactive strategies to ensure accuracy in budgeting. Properly anticipating inflation’s impact on material costs, labour, and fuel is critical to preventing financial strain later in the project. For example, contractors and estimators may want to employ historical data analysis to better predict cost fluctuations.
Using these strategies can help mitigate the unpredictability of inflation and ensure that construction firms are better prepared to manage rising costs. The next section will explore the supply chain challenges faced by the construction industry, focusing on how inflation disrupts the timely procurement of materials and the potential bottlenecks that occur due to these economic pressures.
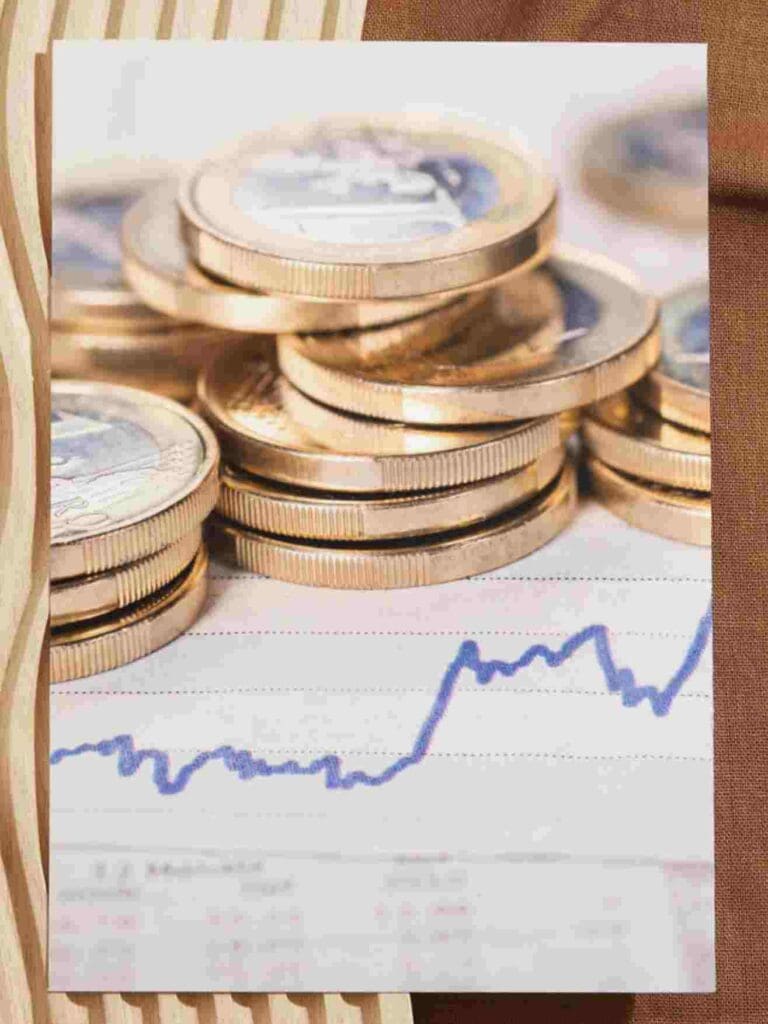
Strategies for Improving Cost Estimation During Inflation
While inflation poses significant challenges for construction cost estimation, there are several strategies that can help mitigate these challenges and improve forecasting accuracy.
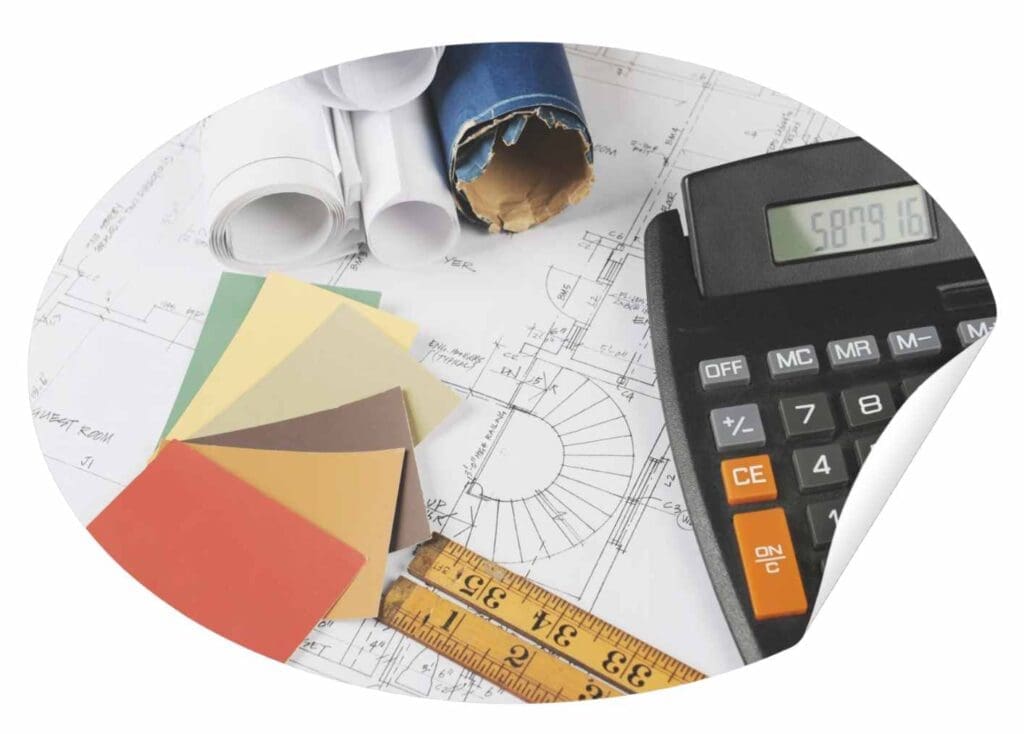
1. Use Historical Data for Trend Analysis
One of the most effective ways to improve cost estimation accuracy is to use historical data to analyse trends over time. By reviewing previous projects and the way inflation has affected material, labour, and transportation costs, estimators can gain valuable insights into cost fluctuations. Trend analysis enables them to predict future cost increases with greater precision, making cost estimation more reliable.
By using historical data, contractors can understand how inflation has historically impacted specific areas of construction and incorporate this knowledge into their cost estimation processes. This approach allows for better preparation when facing rising costs during the project.
2. Include Contingency Budgets
To manage the unpredictability of inflation, it’s advisable to include contingency budgets in cost estimates. A contingency budget is a financial reserve set aside to cover unexpected price increases or unforeseen costs that arise during construction. Typically, a contingency budget of 5% to 10% of the total project cost is recommended to absorb inflation-related increases.
A contingency budget acts as a safety net for construction projects, ensuring that unanticipated price hikes do not derail the project or lead to financial strain. It helps keep the project on track, even when inflation causes unexpected cost increases for materials, labour, or fuel.
3. Lock in Prices Early
One strategy to manage the impact of inflation on material prices is to lock in prices early. Contractors can negotiate fixed-price contracts with suppliers or purchase materials in advance to avoid price increases later in the project. This strategy is especially effective for large projects where material costs can fluctuate significantly over time.
Securing materials early allows construction firms to mitigate the risk of inflation and ensure predictable project costs. This can be particularly important when working on long-term projects that span several months or years, as material prices may change significantly during that time.
4. Monitor Market Trends Regularly
Regularly monitoring market trends is crucial for managing inflation’s impact on construction costs. Keeping an eye on key material costs, fuel prices, and labour rates helps construction firms adjust their estimates and expectations as needed. Staying informed about market shifts enables contractors to identify price trends early, giving them a better chance to adjust their budgets accordingly.
Being proactive in tracking market conditions can help reduce the likelihood of underestimating costs due to unforeseen price fluctuations. By staying informed, contractors can make more accurate predictions and adjust their cost estimates to reflect current conditions.
5. Foster Strong Supplier Relationships
Building strong relationships with suppliers is an important strategy for managing inflation-related price increases. Strong supplier relationships can offer several advantages, such as securing better terms, priority access to materials, and negotiating flexibility in pricing. A reliable supplier network can also help construction firms manage material availability, reducing the risk of delays or cost overruns due to inflation-driven supply shortages.
By cultivating these relationships, construction companies can gain more control over material prices and procurement, helping them better manage inflation’s impact on project costs.
This section has explored the key challenges posed by inflation in construction cost estimation and offered strategies to help construction firms navigate these challenges effectively. In the next section, we will delve into the broader supply chain issues caused by inflation, focusing on the disruptions and delays that construction companies face in sourcing materials and managing logistics.
The Impact of Inflation on Supply Chains in Construction
As inflation continues to rise, its impact on the construction industry extends far beyond the immediate costs of materials and labour. One of the most significant effects is on the construction supply chain. With inflation driving up the costs of raw materials, fuel, and labour, it’s becoming increasingly difficult for construction firms to maintain the flow of goods and services needed to keep projects on track. In this section, we will explore the challenges inflation poses to construction supply chains, the effects on material procurement, and the strategies for managing these disruptions.
Disruptions in Material Procurement
One of the most direct impacts of inflation on construction supply chains is the disruption in material procurement. As inflation increases, the cost of raw materials such as steel, timber, concrete, and other construction essentials rises. This leads to price hikes that can affect both the short-term and long-term supply of materials, often causing delays or shortages.
When material prices fluctuate unpredictably, construction firms may struggle to secure the necessary supplies within their budgeted costs. This volatility can lead to supply chain disruptions, as contractors may be forced to renegotiate contracts with suppliers or look for alternative sources of materials. In some cases, materials become unavailable, resulting in project delays and additional costs for procurement.
Material shortages can also increase competition for limited resources, driving prices even higher. When suppliers are unable to meet demand, construction firms must act quickly to secure the materials they need, sometimes paying premium prices for availability.
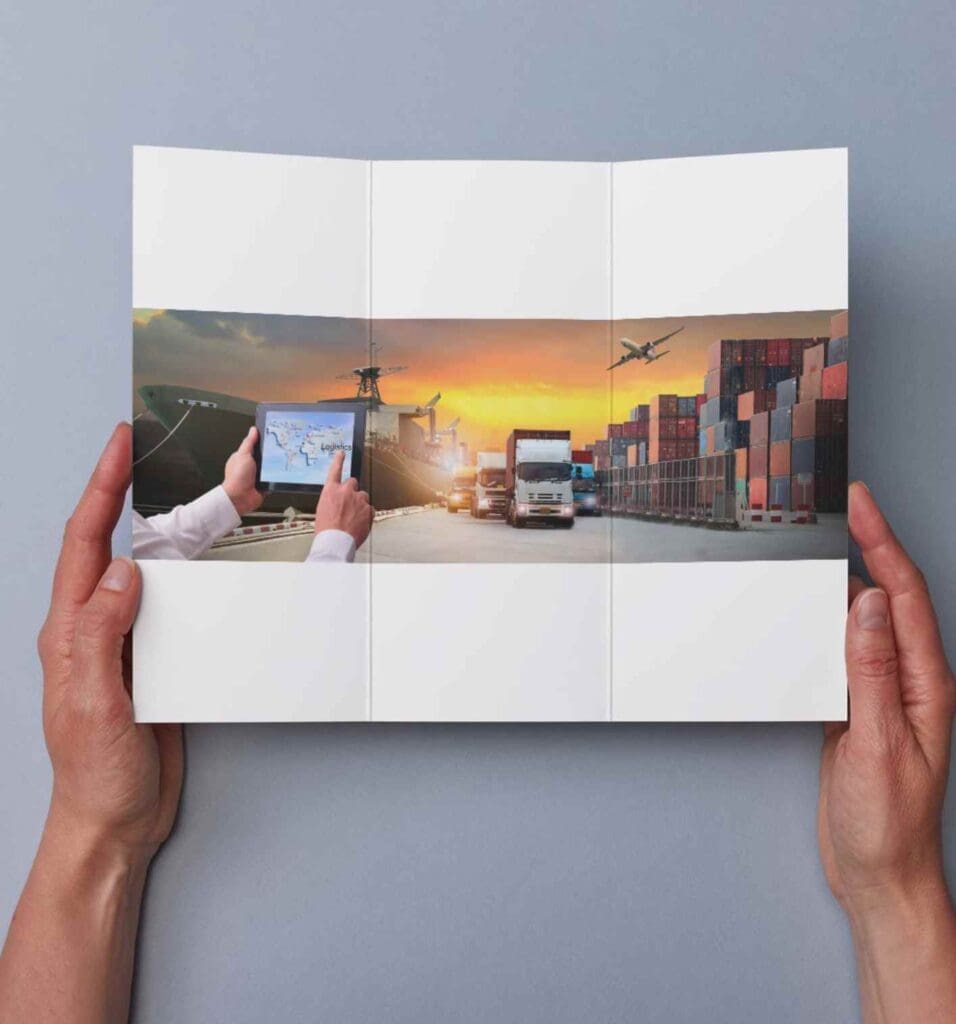
The Role of Transportation Costs in Supply Chain Challenges
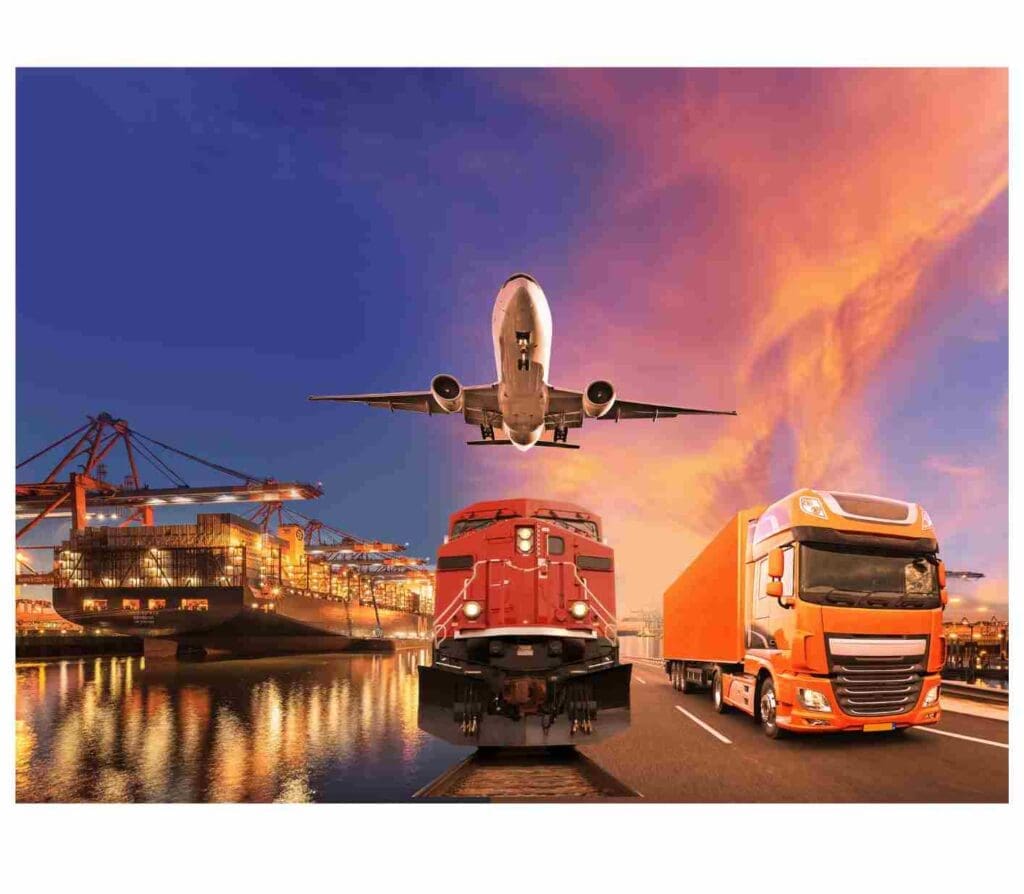
Transportation costs are another major factor affected by inflation. As fuel prices rise, so do the costs of transporting materials to and from construction sites. This impact is especially pronounced for large-scale projects, where transportation costs can make up a significant portion of the overall budget.
Additionally, inflationary pressures on fuel prices can lead to shipping delays as logistics companies struggle to cope with rising operating costs. For construction companies, this can result in delays in receiving essential materials and equipment, causing knock-on effects on project timelines and overall delivery. Managing transportation costs effectively and ensuring timely deliveries becomes more challenging during inflationary periods.
To mitigate these risks, construction firms must stay on top of fuel price trends and adjust their supply chain strategies accordingly. This might involve renegotiating transportation contracts, seeking alternative transportation routes, or investing in more efficient delivery systems.
Labour Shortages and Workforce Costs
Inflation is also putting pressure on the construction workforce, with rising wages and a shortage of skilled labour becoming increasingly common. Construction companies are experiencing significant difficulties in hiring and retaining workers as inflation drives up the cost of living. As wages rise, contractors are forced to increase their budget for labour costs, which directly impacts the overall project budget.
Labour shortages are exacerbated by the increasing cost of training and upskilling workers. As skilled tradespeople become more expensive, firms may struggle to maintain the same workforce levels, leading to delays in construction schedules. This labour cost inflation not only impacts construction firms’ ability to hire but also affects the efficiency of supply chains as fewer workers are available to handle materials, manage deliveries, or oversee project phases.
Additionally, inflation may lead to a rise in fringe benefits such as insurance premiums and health benefits, which adds further costs to managing a workforce. Construction firms need to plan for these rising costs and find innovative ways to attract and retain skilled labour.
Increased Competition for Limited Resources
Another effect of inflation is heightened competition for limited resources. As material prices rise, construction companies may find themselves competing with other industries and projects for the same materials and suppliers. This is particularly true in periods of high demand, such as during large infrastructure booms or post-disaster reconstruction efforts.
When supply chains are under pressure, materials may be allocated based on priority, and construction companies with lower purchasing power or smaller projects may face delays or price hikes due to this increased competition. In some cases, this results in a bidding war for materials, further inflating prices and extending lead times.
Construction firms can overcome this challenge by building strong relationships with suppliers, as well as engaging in forward buying—securing materials ahead of time to avoid shortages. However, with inflation creating an unstable environment, these strategies are not always foolproof.
The Challenge of Managing Project Schedules
Inflation-induced supply chain disruptions and material shortages can severely affect project schedules. Delays in material procurement, transport, and workforce availability can push back deadlines, sometimes by weeks or months. This creates a ripple effect, as subsequent tasks may need to be rescheduled, and construction timelines become difficult to manage.
With inflation driving up the costs of everything from raw materials to labour, contractors may struggle to deliver projects on time and within budget. This becomes particularly difficult when multiple supply chain disruptions occur simultaneously, as it can create a backlog of tasks that ultimately delay project completion.
Construction firms can address this issue by adopting more flexible project management practices, including contingency planning for unexpected delays, and adjusting timelines as needed to account for inflation-related challenges. Additionally, real-time tracking of material availability and shipping schedules can help firms stay ahead of potential disruptions.
Managing the Impact of Inflation on the Entire Supply Chain
Inflation is not just a financial issue; it is a logistical one as well. To successfully navigate the challenges of an inflationary environment, construction companies must adopt a more holistic approach to managing their supply chains. This includes closely monitoring both the costs and availability of materials, transportation, and labour, while also preparing for potential supply chain disruptions by building in contingency plans.
Construction companies can also look into integrating digital tools that help streamline the management of procurement and logistics. These tools allow firms to track inventory levels, manage orders, and forecast potential delays, providing greater transparency and better control over the supply chain process.
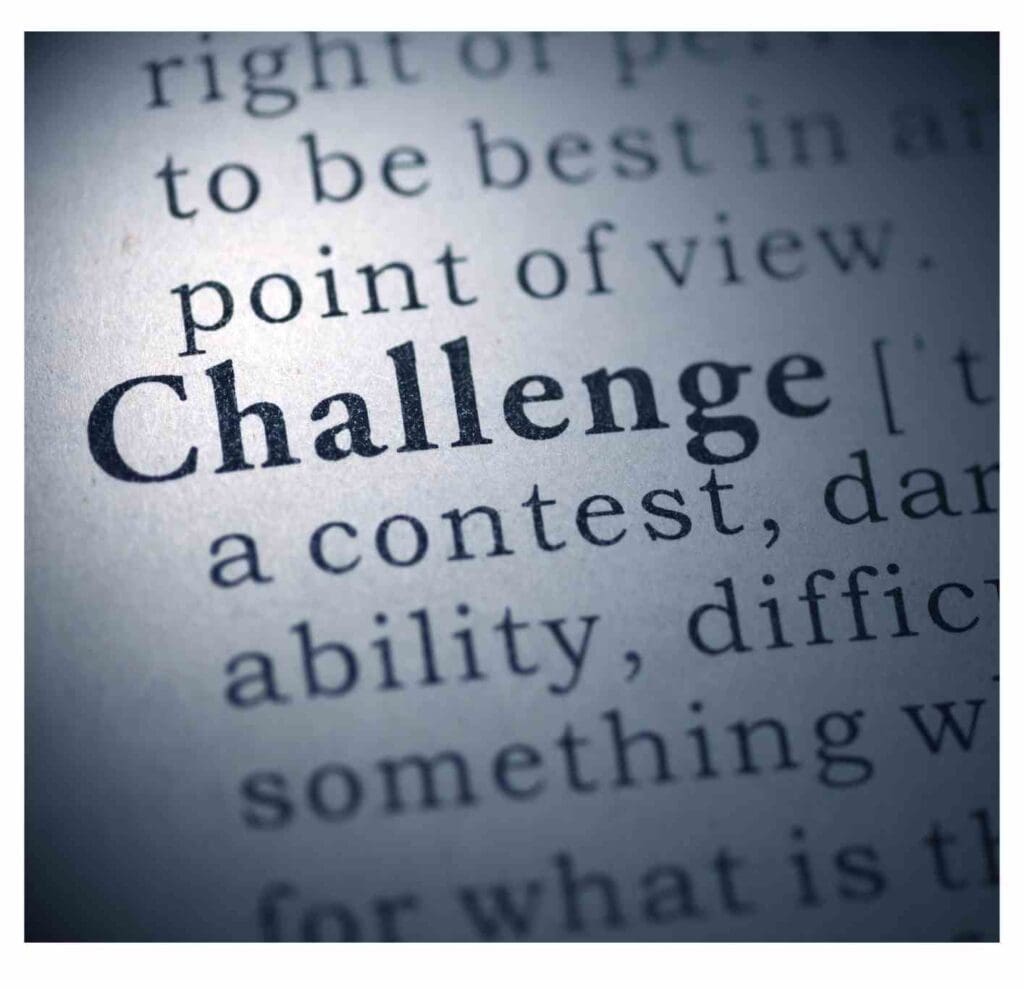
Diversifying Supply Sources
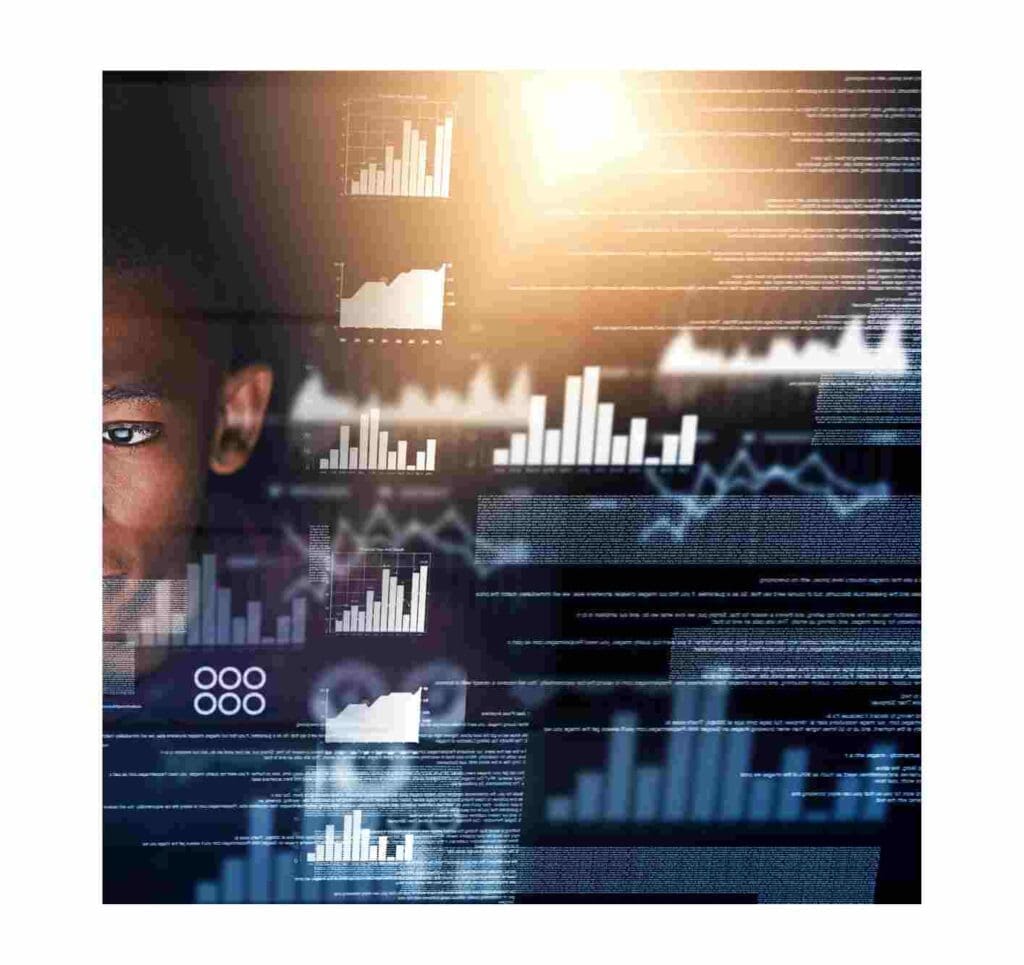
As inflation makes it difficult to rely on a single source for materials and equipment, construction firms may benefit from diversifying their construction supply chain. By sourcing materials from multiple suppliers and regions, companies can reduce their reliance on a single vendor and avoid disruptions caused by regional inflationary pressures. This approach also provides construction companies with bargaining power, allowing them to negotiate better terms and mitigate the risk of price increases within the construction supply chain.
Building a resilient construction supply chain that can adapt to inflation requires forward planning, flexibility, and effective relationship management with suppliers. By focusing on diversification and contingency planning, construction firms can reduce the impact of inflation on their projects and maintain a steady flow of materials and resources within the construction supply chain.
Conclusion
Inflation has far-reaching effects on the construction supply chain, with significant implications for material costs, labour, transportation, and overall supply chain management. As inflation causes raw material prices to rise, labour costs to increase, and logistics to become more complex, construction companies face a range of challenges. However, by adopting proactive strategies, such as locking in prices early, diversifying supply sources, and fostering strong supplier relationships, firms can better navigate the turbulence caused by inflation in the construction supply chain.
Construction cost estimation and construction supply chain management must evolve to address these challenges. By staying informed, using historical data, and incorporating contingency budgets, contractors can better anticipate the effects of inflation and make more accurate forecasts for their projects. Inflation may be an unavoidable force, but with the right tools and strategies, construction firms can mitigate its impact on the construction supply chain and continue to thrive in an ever-changing economic landscape.
FAQ
1. What is the construction supply chain and why is it important?
The construction supply chain refers to the series of processes involved in acquiring, storing, and delivering the materials, equipment, and services needed for a construction project. It includes suppliers, manufacturers, transportation companies, and construction contractors. An effective construction supply chain is essential for ensuring timely delivery, cost management, and the successful completion of construction projects.
2. How does inflation affect the construction supply chain?
Inflation directly impacts the construction supply chain by increasing the costs of raw materials, transportation, and labour. As the cost of goods and services rises, contractors often face challenges in securing materials within their budget, leading to potential delays and increased project costs. The impact of inflation on the construction supply chain is significant, making it more difficult for firms to predict costs and manage their procurement strategies.
3. What are the key challenges in managing the construction supply chain during inflation?
During periods of inflation, the construction supply chain faces several challenges, including:
- Material shortages due to increased demand and limited supply.
- Rising transportation costs as fuel prices increase.
- Labour shortages and higher wages.
- Price volatility of raw materials and products. These issues make it harder to maintain a smooth flow of goods, which can lead to delays and cost overruns.
4. How does inflation impact material costs in construction?
The impact of inflation on material costs in construction is substantial. As inflation rises, the prices of key materials such as steel, timber, concrete, and aggregates increase. This can significantly raise the overall cost of a construction project, leading to adjustments in pricing, timelines, and sometimes even project scope. Managing the construction supply chain becomes more complex as material costs fluctuate unpredictably during inflationary periods.
5. What steps can construction companies take to mitigate the impact of inflation on the supply chain?
Construction companies can take several steps to mitigate the impact of inflation on the construction supply chain, such as:
- Securing long-term contracts with suppliers to lock in prices.
- Diversifying suppliers to avoid reliance on a single source.
- Forecasting future material costs and adjusting budgets accordingly.
- Building strong relationships with suppliers to ensure reliability and stability. These strategies help ensure that material costs remain as predictable as possible, despite inflation’s effects on the supply chain.
6. How can inflation affect project timelines in construction?
The construction supply chain plays a crucial role in meeting project deadlines. Inflation causes fluctuations in material prices, transport costs, and labour wages, which can delay the availability of materials and workforce. This delay often leads to rescheduled deliveries, labour shortages, and sometimes a slower rate of project progress. Consequently, construction projects may face extended timelines, which may be exacerbated by supply chain disruptions caused by inflation.
7. How can contractors handle rising material costs in construction during inflation?
To handle the rising material costs in construction due to inflation, contractors can:
- Negotiate fixed-price contracts with suppliers to lock in material costs.
- Source materials from alternative suppliers to ensure competitive pricing.
- Purchase materials in bulk to take advantage of lower prices before they rise further.
- Reevaluate project scope to adjust for cost increases. This approach helps construction firms better manage their budgets and avoid significant financial impacts due to inflation.
8. What effect does inflation have on the construction supply chain’s logistics?
Inflation increases fuel prices, which directly impacts the construction supply chain’s logistics. Higher fuel costs increase transportation expenses, which can lead to delays in material deliveries. Transportation companies may face difficulties in maintaining schedules, affecting the timely arrival of materials at construction sites. With material costs in construction on the rise, managing logistics efficiently becomes even more critical during inflationary periods.
9. How does inflation affect labour costs in the construction supply chain?
The impact of inflation extends to labour costs in the construction supply chain. As the cost of living increases, workers demand higher wages to keep up with inflation, which can raise overall labour costs for construction companies. Labour shortages may also become more prevalent, as the cost of hiring skilled workers rises, potentially delaying projects and increasing the need for temporary or contract staff.
10. How can construction companies manage supply chain disruptions caused by inflation?
To manage supply chain disruptions caused by inflation, construction companies should:
- Monitor price trends for materials and fuel regularly.
- Diversify suppliers to ensure multiple sources of materials.
- Invest in advanced supply chain management software to improve forecasting and tracking.
- Maintain strong relationships with key suppliers to secure preferential pricing and delivery schedules. By proactively managing the construction supply chain, companies can reduce the impact of inflation on their projects.
11. Why is forecasting essential for managing material costs in construction during inflation?
Forecasting is crucial for managing material costs in construction during inflation because it helps construction companies anticipate price increases and adjust their budgets accordingly. Accurate forecasts allow for better decision-making in procurement, reducing the likelihood of unexpected cost escalations. When companies are able to predict price trends in the construction supply chain, they can plan accordingly and negotiate better contracts with suppliers.
12. What is the impact of inflation on long-term construction projects?
For long-term construction projects, the impact of inflation on the construction supply chain can be significant. Materials and labour costs may increase over time, which could lead to budget overruns. Additionally, delays caused by inflation-related disruptions in the supply chain can affect the overall timeline of the project. Contractors need to build flexibility into their budgets and schedules to accommodate these potential cost fluctuations.
13. How does inflation influence the availability of raw materials in the construction supply chain?
Inflation can reduce the availability of raw materials in the construction supply chain by creating uncertainty in pricing and supply. When demand outpaces supply or when the cost of production rises due to inflation, manufacturers may be unable to provide the needed materials at the required quantities. This forces contractors to search for alternative sources, often at higher prices or with longer lead times.
14. How can contractors ensure accurate cost estimation in construction during inflation?
To ensure accurate cost estimation in construction during inflation, contractors should:
- Use historical data to predict material and labour cost trends.
- Include contingency budgets to account for inflationary increases in project costs.
- Regularly update cost estimates to reflect the current state of the construction supply chain.
- Work closely with suppliers to get updated pricing and availability forecasts. These strategies help contractors mitigate the effects of inflation on project costs and improve the accuracy of their cost estimations.
15. What are the most affected materials in the construction supply chain due to inflation?
Key materials in the construction supply chain that are most affected by inflation include:
- Steel: One of the most volatile materials, with price fluctuations driven by global demand and supply chain disruptions.
- Timber: The cost of lumber has been subject to rapid price increases due to increased demand and supply chain constraints.
- Concrete: The cost of concrete can rise with inflation due to increases in energy prices and raw material costs. These materials play an essential role in construction, and their price hikes have a direct impact on material costs in construction, making it more difficult to control budgets during inflation.
Thank you for your visit, and welcome to the construction home