Blog Post – The success of any construction project relies heavily on meticulous planning, communication, and coordination during its various phases. This article will delve into the critical elements of the combustible cladding replacement pre-construction, construction, and post-construction phases of a project, focusing on responsibilities, required tasks, and the importance of collaboration between engineers, architects, and contractors. These insights are especially important for those involved in façade replacements and combustible cladding replacement works, as compliance and safety are key to a project’s long-term success. Understanding the process of combustible cladding replacement ensures that all phases are handled efficiently, and that fire safety measures and regulatory standards are met throughout the entire project.
Section 1: Pre-Construction Phase of combustible cladding replacement
Understanding the combustible cladding replacement Pre-Construction Phase
The pre-construction phase is one of the most critical stages in a building project. It sets the foundation for what follows during construction and determines whether the project will run smoothly or face complications down the line. During this phase, thorough planning, site inspections, design development, and compliance assessments take place, ensuring all parties understand their roles and responsibilities. Let’s explore the key tasks in this phase.
Initial Documentation Review
The first step in the pre-construction phase involves the review of initial documentation by key professionals such as the architect, façade engineer, fire engineer, and Sydney Contracting Engineers (SCE). These experts assess documents, architectural plans, and previous reports to get an understanding of the project’s scope, any potential risks, and the requirements for the site. This collaborative review process ensures that all stakeholders are aligned on expectations and standards.
Importance of Combustible cladding replacement Site Visit and Inspection
A site visit and inspection by the fire engineer are essential to visually assess the current state of the building. This visit allows the engineer to identify any visible concerns related to fire safety and compliance, and to ensure that the location’s unique characteristics are considered in the subsequent design and construction stages. The fire engineer’s early involvement can help prevent safety oversights that may become costly down the line.
Assessing Existing Substructure Conditions of cladding
An essential task during this phase is the inspection of removed panels and the review of the existing substructure. This involves:
1. Evaluating the substructure details
2. Checking for signs of corrosion
3. Identifying any waterproofing issues
This inspection of Combustible cladding replacement is typically carried out by the façade engineer, whose responsibility is to ensure that the existing substructure can support the replacement combutible cladding system without any issues. Early detection of structural or waterproofing problems allows for timely solutions before construction begins, saving both time and money.
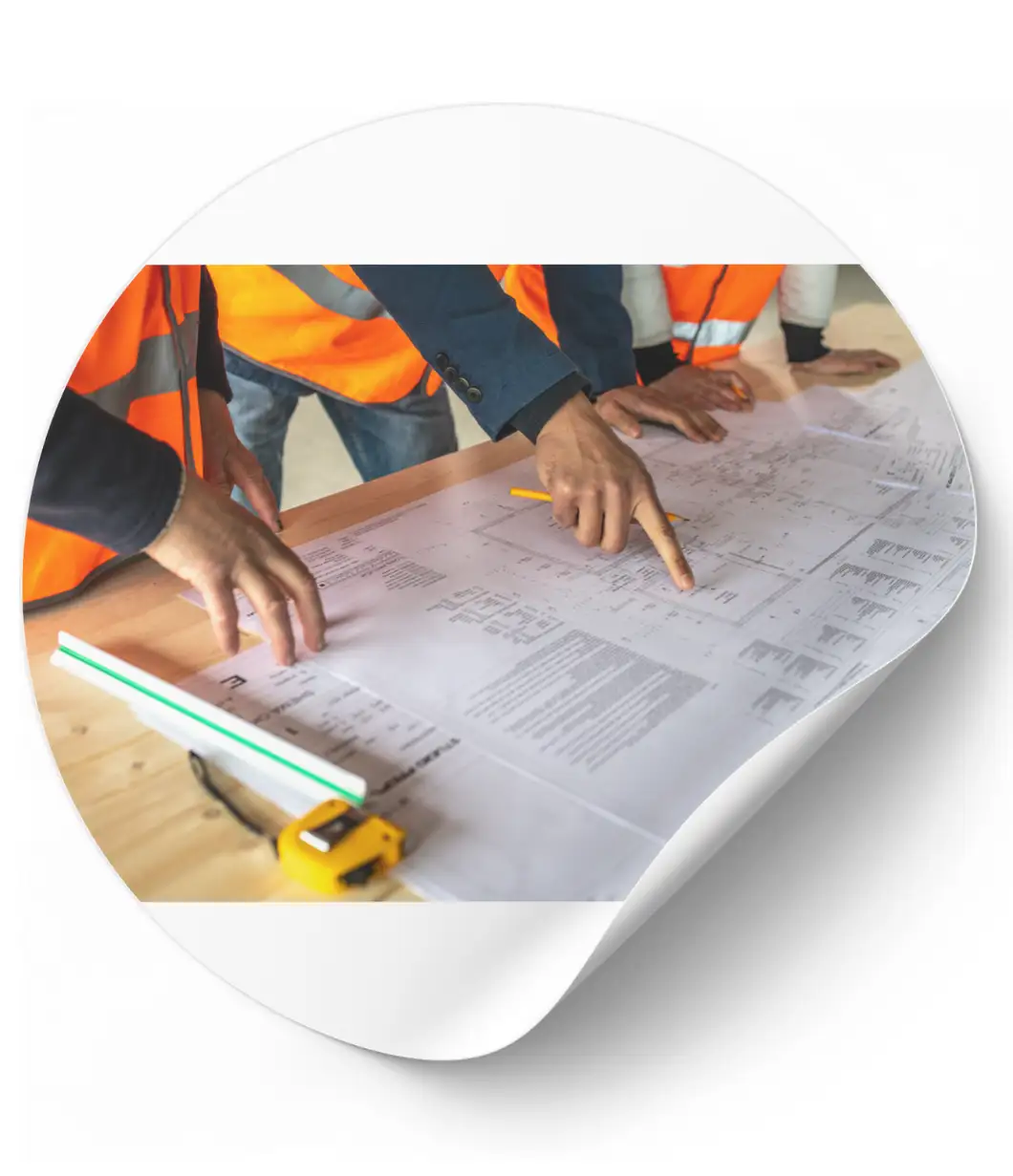
Façade Assessment: A Multi-Faceted Approach

A comprehensive façade assessment conducted by the façade engineer is crucial to understanding the current state of the building’s exterior. This assessment includes:
Thermal performance: Ensuring the building maintains energy efficiency
Condensation risks: Addressing potential moisture build-up within the cladding system
Waterproofing: Evaluating if the current waterproofing measures are adequate
Substructure conditions: Confirming the structural integrity of the façade
Façade assessments ensure that all design aspects are suitable for the environmental and structural demands of the project.
Specification of Materials
Material selection is a crucial aspect of the pre-construction phase. SCE (Accredited DBP) is responsible for specifying materials that meet all relevant building codes and safety standards, ensuring durability and compatibility with the existing building structure. Material specifications must consider the thermal, acoustic, and fire performance of the cladding system.
Architectural Plans and Specifications
The architect plays a vital role in developing detailed architectural plans and specifications. These include:
1. Site plans
2. Floor plans
3. Wall details
4. Elevations
Cross-sectional drawings, showcasing the exact details of the cladding system
Clear and accurate documentation at this stage minimises the risk of errors during construction and helps streamline communication between all involved parties.
Assessing Structural Stability and Loading
The façade engineer is responsible for conducting a loading assessment to ensure the substructure can safely support the new cladding materials. This assessment includes calculations to verify that the structure can withstand the loads imposed by the new materials, ensuring safety and compliance with local building codes.
Façade Concept and Detailed Design
Once the structural and material assessments are complete, the façade engineer develops a façade concept design that outlines the overall appearance and functionality of the new cladding system. Following this, a detailed design is created, which includes:
Design workshops held either online or in Sydney
Detailed sketches of each element of the façade
These workshops and designs ensure all stakeholders have a clear vision of the final product and any concerns are addressed before construction begins.
Reviewing the New Cladding Material
The fire engineer is tasked with reviewing the new cladding material, focusing on how it interacts with the primary wall structure. This is particularly important for ensuring that the new materials meet fire safety standards. The fire engineer also reviews the material data sheets, test reports, and proposed methods of installation to verify that everything is in line with building safety regulations.
Fire Engineering Design and Compliance Review
Fire safety is a critical concern in any construction project, particularly in combustible cladding replacement works. The fire engineer is responsible for preparing a Performance-Based Design Brief and a Fire Engineering Report, both of which outline the fire safety strategy for the project. These documents ensure that the cladding system meets all fire safety regulations and can perform effectively under fire conditions.
Additionally, the fire engineer prepares a Fire Engineering Compliance Statement, confirming that the cladding system and installation method are compliant with Australian fire safety standards.
Design Compliance and Certification
Both the architect and the façade engineer must issue their respective Design Compliance Statements and Design Certificates, verifying that the project adheres to all relevant building codes and standards. This step ensures that the design phase is completed with all necessary approvals in place before moving forward to the construction phase.
Site Management Procedures
Proper site management procedures are crucial for maintaining safety and quality control during construction. SCE (Accredited DBP) is responsible for preparing:
A construction site plan detailing the layout of the site
A safety management plan that outlines safety protocols for workers and site visitors
A quality management plan to ensure the construction meets all required standards
An environmental management plan that addresses how the project will minimise its environmental impact
By developing comprehensive management plans, SCE ensures that the construction process will be safe, efficient, and environmentally conscious.
NSW Planning Portal Submission
Once all documentation and designs are complete, the architect and SCE (Accredited DBP) collaborate to submit the regulated design set to the NSW Planning Portal for approval. This step is essential for obtaining the necessary permits and authorisations before construction can commence. The planning portal submission includes architectural drawings, material specifications, and compliance reports from the fire and façade engineers.
In the next section, we will delve into the construction phase, covering the practical steps involved in the execution of a project and the responsibilities of the key stakeholders during this critical stage.

Continue with Section 2 to dive deeper into the construction phase, or check out more on how to ensure compliance and safety in building projects Read more.
Section 2: The Construction Phase – Bringing Plans to Reality

Navigating combustible cladding replacement the Construction Phase
The construction phase is where meticulous planning transforms into tangible progress. At this stage, the roles of Sydney Contracting Engineers (SCE), architects, façade engineers, and fire engineers come together in unison to execute the pre-approved plans for combustible cladding replacement. Coordination, precision, and quality control ensure that every step of the combustible cladding replacement process complies with safety standards, regulatory requirements, and project timelines. The team works together to ensure that all materials and systems meet fire safety codes. Let’s break down the critical tasks and responsibilities within this phase of combustible cladding replacement.
Road Occupancy Licence and Type A Hoarding Applications
Before construction can commence, certain approvals must be obtained. SCE is responsible for applying for a Road Occupancy Licence if works impact public roads, ensuring minimal disruption to traffic flow. Additionally, a Type A Hoarding Application is lodged to install protective barriers for pedestrian safety around the worksite. These measures prioritise safety and compliance during the construction process.
Pre-Construction Preparations and Site Mobilisation
Pre-Construction Dilapidation Report
A pre-construction dilapidation report, conducted by SCE, documents the current condition of surrounding structures and surfaces, such as roads, pathways, and adjacent buildings, before the commencement of combustible cladding replacement works. This report is critical in identifying any pre-existing damage and protecting all parties in case disputes arise during or after combustible cladding replacement. By thoroughly documenting the conditions before starting combustible cladding replacement, potential issues can be addressed early on, ensuring smoother project execution and mitigating risks for everyone involved.
Site Mobilisation and Resource Management
The site is then mobilised by SCE, where construction equipment, materials, and resources are delivered and organised. This includes setting up:
1. Site offices
2. Tool storage areas
3. Safety barriers
Furthermore, SCE manages the supply of small tools, signage, and consumables needed to support on-site operations.
Utility Surveying and Locating Services
Before any physical works begin, surveying and utility locating is conducted by SCE to identify underground services, such as water, gas, electricity, and communication lines. This process prevents accidental damage during excavation or installation of the cladding system.
Installation and Testing of Access Methods
Engineering and Mobilisation of Access Systems
Safe and efficient access is critical for façade works. SCE oversees the engineering, mobilisation, and installation of access systems, such as scaffolding, elevated work platforms (EWPs), or rope access systems. Once installed, all access points are tested and tagged to confirm their safety and compliance with WHS standards.
Access System Management
Throughout the project, SCE manages:
1. Hiring and relocation of access systems as required
2. Safe dismantling and demobilisation once works are completed
This meticulous access management ensures minimal disruption and maximum safety for workers and surrounding areas.
Removal of Existing Façade and Cladding Materials
The next major milestone is the removal and storage of existing façade elements, followed by the removal and disposal of non-compliant cladding materials. SCE adheres to strict waste disposal protocols to ensure environmentally responsible practices while doing the removal and disposal of non-compliant cladding materials.
Inspection and Modification of the Substructure
Repairing the Substructure
Once the old façade is removed, the existing substructure, including framing, sub-frames, insulation, and waterproofing, is assessed. If issues such as corrosion, structural weaknesses, or waterproofing failures are identified, SCE undertakes necessary cladding repairs or modifications to restore stability and compliance.
Façade Engineer Site Inspection
The façade engineer conducts a thorough inspection at this stage to ensure the substructure is ready for the installation of the new façade elements. This step is crucial for avoiding delays or costly errors further down the line.
Supply and Installation of Replacement Systems
Installing Replacement Framing and Insulation
Once the substructure has been prepared, SCE supplies and installs:
1. Replacement framing and sub-frames
2. Sarking (a protective membrane)
3. Insulation systems to enhance thermal and acoustic performance
The installation process is executed with precision to ensure longevity, durability, and compliance with design specifications.
Installing New Cladding Materials
With the substructure ready, the new cladding materials are supplied and installed by SCE. This is a pivotal stage of the project, as the façade contributes to both the aesthetics and functionality of the building. All cladding materials must align with the approved architectural drawings, façade engineer designs, and fire safety regulations.

On-Site Inspections and Quality Assurance

Fire Engineer Oversight
The fire engineer conducts site inspections during the delivery and installation of cladding materials. These inspections of cladding panel confirm that the new façade meets fire safety standards and that the interface with the primary wall structure is seamless.
Quality Testing and Performance Validation
To guarantee that all elements of the façade perform as intended, SCE conducts rigorous testing of installed systems. This includes checks for:
Waterproofing performance
Thermal insulation compliance
Structural stability
Reinstatement of Façade Elements
Any previously removed façade elements, such as windows, vents, or decorative panels, are reinstated by SCE to ensure the building returns to its complete and functional state. This task requires careful handling of cladding panels to avoid damage and ensure proper integration with the new cladding system.
Fire Safety Upgrades
Where required, SCE installs or modifies fire safety measures to ensure compliance with the latest regulations. These measures may include:
Fire-resistant seals
Smoke barriers
Fire-rated façade components
These upgrades enhance the overall safety and resilience of the building.
Access System Demobilisation and Site Clean-Up
Once the façade works are completed, SCE oversees the dismantlement and removal of access systems, ensuring the site is demobilised safely and efficiently. Following this, the site undergoes a thorough clean-up to restore it to a professional, finished standard.
Post-Construction Dilapidation Report
To close out the construction phase, SCE prepares a post-construction dilapidation report, documenting the condition of surrounding structures and surfaces after works have been completed. This report helps to resolve any disputes regarding potential damages, providing a clear comparison against the initial dilapidation report.
Finalising the Construction Phase
The successful completion of the construction phase depends on the combined efforts of all parties involved. By adhering to strict safety standards, quality control processes, and regulatory compliance, the project progresses seamlessly into the final post-construction phase.
In the next section, we’ll explore the final stage of the project: post-construction compliance and certification, ensuring the building is safe, functional, and ready for handover.
For further insights on façade safety and compliance, check out SafeWork NSW guidelines. Stay tuned for the final section of this comprehensive guide.
Section 3: The Post-Construction Phase – Ensuring Compliance and Project Completion
Finalising the Project – Post-Construction Essentials
The post-construction phase marks the final leg of the project, where the focus shifts to ensuring compliance, verifying quality, and delivering a safe, functional façade system. At this stage, the collaborative work of SCE, fire engineers, façade engineers, and architects culminates in a completed project ready for client handover. This phase is critical for meeting legal requirements and providing assurance that all construction works align with building codes, fire safety standards, and architectural intent.
Final Compliance Certification
The Role of the Fire Engineer
The final compliance certification is one of the most critical deliverables in the post-construction phase. The fire engineer performs a detailed review of all installed façade systems and associated fire safety measures. This ensures that the new cladding and façade components meet the strict regulatory standards set forth under the National Construction Code (NCC) and other applicable guidelines.
The fire engineer confirms that the materials, design, and installation provide the intended fire resistance and safety performance, issuing the Final Compliance Certificate as verification.
Site Inspection Report
The fire engineer also conducts a comprehensive site inspection report, which documents:
The installation and performance of the cladding system
Compliance with fire safety measures
Proper integration with existing structures
This report ensures that every aspect of the façade replacement or repair has been executed to the highest standards, offering peace of mind to building owners, tenants, and stakeholders.
Quality Assurance and Project Handover
Meeting Design Specifications
Before formal handover, the façade engineer reviews the final installation to confirm alignment with all architectural plans and design certificates. This step validates that the façade meets structural, thermal, waterproofing, and aesthetic requirements outlined during the pre-construction phase.
Ensuring a Functional and Safe Façade
Through a final quality assurance process, SCE ensures that:
1. The cladding materials and substructure are secure and durable
2. All waterproofing systems are functional
3. Structural stability has been achieved
4. Thermal and condensation performance meet design intent
This thorough quality check guarantees that the completed façade system will perform reliably for years to come.

Post-Construction Clean-Up and Final Presentation
Once all inspections and certifications are complete, SCE undertakes a final site clean-up to ensure the area is left in pristine condition. The building is then formally presented to the client with all necessary documentation, certifications, and performance reports.
Delivering Comprehensive Documentation

At the project’s conclusion, a comprehensive set of documentation is handed over to the client. This includes:
1. Final Compliance Certification – Verifying fire safety compliance
2. Façade Engineer Design Certificate – Confirming structural integrity and performance
3. Site Inspection Reports – Documenting the condition of the façade post-construction
4. Material Specifications – Outlining materials used and their performance characteristics
5. Maintenance Guidelines – Providing instructions for ongoing care and inspection of the façade system
This documentation ensures transparency and gives clients the tools needed to maintain the integrity of their building for the long term.
Importance of a Post-Construction Maintenance Plan
While the façade installation marks the end of construction, the long-term success of the system depends on proactive maintenance and monitoring. Clients are encouraged to implement a regular maintenance plan, which includes:
1. Routine inspections for signs of damage, corrosion, or wear
2. Cleaning schedules to maintain the façade’s appearance
3. Monitoring fire safety systems to ensure ongoing compliance
Proactive maintenance not only prolongs the façade’s lifespan but also reduces the risk of costly repairs in the future.
How SCE Delivers Exceptional Results
Sydney Contracting Engineers (SCE) stands out as a trusted partner in façade projects due to our commitment to:
1. Compliance and Safety: Our team adheres to all NSW building codes, fire safety standards, and quality guidelines.
2. Collaboration: We work closely with architects, façade engineers, and fire engineers to deliver seamless, compliant solutions.
3. Precision and Expertise: Our experienced professionals ensure that every phase of the project – from planning to handover – is executed to the highest standard.
Our approach guarantees that your façade system is safe, compliant, and built to last.
Why Post-Construction Compliance Matters
Ensuring compliance during the post-construction phase is vital for several reasons:
1. Safety: Final inspections and certifications confirm that the façade is fire-resistant, structurally sound, and safe for occupants.
2. Legal Requirements: Non-compliance can lead to significant fines, legal issues, or the need for costly rectification works.
3. Property Value: A fully compliant façade system enhances the value and longevity of the building.
4. Peace of Mind: Clients gain confidence knowing their building meets the highest standards of quality and safety.
The Benefits of Working with SCE
Partnering with Sydney Contracting Engineers offers several key benefits, including:
End-to-End Project Management
From initial documentation review to post-construction certification, SCE manages every phase of your façade project, ensuring a streamlined and stress-free process.
Expertise Across Key Disciplines
Our team collaborates seamlessly with architects, façade engineers, and fire engineers, ensuring compliance and excellence at every step.
Focus on Safety and Compliance
We prioritise safety through rigorous inspections, testing, and adherence to all NSW building laws and SafeWork Australia guidelines.
High-Quality Outcomes
By using premium materials, proven methodologies, and industry-leading expertise, SCE delivers façade systems that combine aesthetics, performance, and longevity.
Conclusion – A Collaborative Path to Success
The pre-construction, construction, and post-construction phases form the backbone of any façade replacement or repair project. Each phase demands careful planning, collaboration, and execution to achieve a safe, compliant, and durable façade system.
Sydney Contracting Engineers, in collaboration with architects, façade engineers, and fire engineers, ensures that every step – from initial assessment to final compliance certification – is carried out to the highest standard.
By working with SCE, clients gain a reliable partner committed to delivering projects that stand the test of time, meet strict safety standards, and enhance the overall value of their building.
Ready to Transform Your Façade?
If you’re considering a façade replacement or remedial project, Sydney Contracting Engineers is here to help. Contact us today to learn more about our comprehensive façade solutions, or explore resources like NSW Government Façade Safety Regulations.
Transform your building with confidence – choose SCE for excellence, safety, and lasting results.
For more updates and insights, visit our blog regularly or speak with one of our experts about your façade project. Sydney Contracting Engineers – Building the future, one façade at a time.
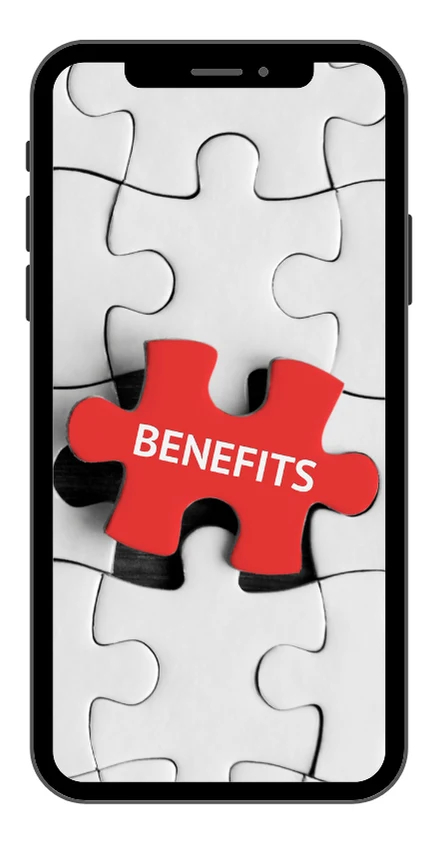
Responsibilities and Deliverables for Replacing Combustible Cladding Across Pre-Construction, Construction, and Post-Construction Phases
Pre-Construction Phase
Item | Description | Responsible |
1 | Initial documentation review | Architect Façade Engineer Fire Engineer SCE |
2 | Site visit and inspection | Fire Engineers |
3 | Inspection of removed panel and review of existing system 1.Details of the substructure 2.Condition of the substructure in terms of corrosion. 3. Any potential issues with waterproofing | Façade Engineer |
4 | Façade assessment Thermal Condensation Waterproofing Substructure | Façade Engineer |
5 | Material specifications | SCE (Accredited DBP) |
6 | Architectural plans, drawings and specifications Site Plan Floor plans Wall details Elevations Cross section showing details of the cladding | Architect |
7 | Assessment of the structural stability of the substructure Loading assessment | Façade Engineer |
8 | Façade concept design | Façade Engineer |
9 | Façade detail design SCE (Accredited DBP) design workshops (online or in Sydney) Detailed sketches for façade items | Façade Engineer |
10 | Review the new cladding material, and interface of the cladding with the primary wall structure | Fire Engineer |
11 | Documentation review of material data sheet, test report and method of proposed cladding replacement | Fire Engineer |
12 | Performance Base Design Brief, Fire Engineering Brief Questionnaire and Fire Engineering Report | Fire Engineer |
13 | Architect Design Compliance Statement | Architect |
14 | Façade Engineer Design Certificate | Façade Engineer |
15 | Fire Engineer Compliance Statement | Fire Engineer |
16 | Site management procedures Construction site plans Safety management plan Quality management plan Environmental management plan | SCE (Accredited DBP) |
17 | Regulated design set | Architect SCE |
18 | NSW planning portal submission | Architect SCE |
Construction Phase
Item | Description | Responsible |
1 | Road Occupancy Licence application | SCE (Accredited DBP) |
2 | Type A Hoarding Application | SCE (Accredited DBP) |
3 | HBCF | SCE (Accredited DBP) |
4 | Authority Fees (Construction Zones, Council Bonds, Ausgrid/Endeavour Energy, Telstra, etc) | SCE (Accredited DBP) |
5 | Pre-construction dilapidation report | SCE (Accredited DBP) |
6 | Site mobilisation | SCE (Accredited DBP) |
7 | Small tools, signs, consumables | SCE (Accredited DBP) |
8 | General waste disposal | SCE (Accredited DBP) |
9 | Surveying and utility locating | SCE (Accredited DBP) |
10 | Installation, and test and tag of anchor points | SCE (Accredited DBP) |
11 | Engineering and delivery of access method | SCE (Accredited DBP) |
12 | Mobilisation and installation of access method | SCE (Accredited DBP) |
13 | Hiring of access method | SCE (Accredited DBP) |
14 | Relocation of access method | SCE (Accredited DBP) |
15 | Removal and storage of existing façade elements | SCE (Accredited DBP) |
16 | Removal and disposal of existing cladding materials | SCE (Accredited DBP) |
17 | Removal, redesign, modification, and repair of existing framing, sub-frame, sub-structure, sarking and insulation | SCE (Accredited DBP) |
18 | Site inspection | Façade Engineer |
19 | design workshops (online or in Sydney) | Façade Engineer |
20 | Supply and installation of replacement framing, sub-frame, sub-structure, sarking and insulation | SCE (Accredited DBP) |
21 | Supply and install of replacement cladding materials | SCE (Accredited DBP) |
22 | Site inspections at the day of cladding materials delivery and installation. | Fire Engineer |
23 | Reinstatement of existing façade elements | SCE (Accredited DBP) |
24 | Testing | SCE (Accredited DBP) |
25 | Install any proposed new or modified fire safety measures | SCE (Accredited DBP) |
26 | Dismantlement and demobilisation of access method | SCE (Accredited DBP) |
27 | Site demobilisation | SCE (Accredited DBP) |
28 | Cleaning and make good | SCE (Accredited DBP) |
29 | Post-construction dilapidation report | SCE (Accredited DBP) |
Post-Construction Phase
Item | Description | Responsible |
1 | Final Compliance Certification | Fire Engineer |
2 | Site inspection report | Fire Engineer |
FAQ
- What is combustible cladding, and why does it need replacement?
Combustible cladding refers to external building materials that can catch fire or spread flames in case of a fire. It poses a significant safety risk and often fails to meet modern building codes. Combustible cladding replacement is necessary to ensure the safety of occupants, meet compliance standards, and prevent catastrophic fire events like those seen globally.
- What steps are involved in the combustible cladding replacement process?
The combustible cladding replacement process involves:
- Pre-Construction Phase: Documentation review, site inspection, façade assessment, and material specifications.
- Construction Phase: Removal of existing cladding, modification of substructures, installation of compliant materials, and fire safety measures.
- Post-Construction Phase: Final compliance certification and inspections to ensure the building meets all regulations.
- How do you manage cladding risks in construction projects?
Managing cladding risks involves a systematic approach:
- Thorough inspections of existing systems to identify risks (corrosion, waterproofing issues).
- Replacing non-compliant materials with approved, fire-safe alternatives during combustible cladding replacement.
- Involving façade and fire engineers to ensure proper assessment and compliance.
- Implementing safety, quality, and environmental management plans during construction.
- Who is responsible for ensuring the cladding compliance process?
The cladding compliance process involves multiple stakeholders:
- Architects: Ensure design compliance and documentation.
- Façade Engineers: Assess structural stability, façade systems, and performance.
- Fire Engineers: Review fire safety measures and certify compliance.
- Contractors (like SCE): Execute combustible cladding replacement and site management procedures.
- What are the key phases of a combustible cladding replacement project?
A combustible cladding replacement project is divided into three phases:
- Pre-Construction: Planning, façade design, inspections, and material selection.
- Construction: Cladding removal, substructure repair, and installation of compliant materials.
- Post-Construction: Final inspections, compliance certification, and reports to confirm safety.
- How does the cladding compliance process ensure building safety?
The cladding compliance process ensures safety by:
- Identifying non-compliant materials through detailed inspections.
- Removing hazardous cladding and replacing it with certified, fire-resistant alternatives during combustible cladding replacement.
- Implementing fire engineering measures and quality assurance to ensure compliance with Australian building standards.
- What role does a façade engineer play in combustible cladding replacement?
A façade engineer plays a critical role by:
- Inspecting and assessing the existing façade system (thermal performance, waterproofing, and structural stability).
- Designing the replacement façade system and ensuring it integrates seamlessly with the building structure.
- Certifying that the replaced cladding meets regulatory and safety standards during combustible cladding replacement.
- How long does a combustible cladding replacement project take?
The duration of a combustible cladding replacement project depends on factors such as building size, complexity, and site conditions. Generally, the timeline includes pre-construction planning, phased construction for safe cladding removal and replacement, and post-construction certification, which can take anywhere from weeks to several months.
- What materials are used for combustible cladding replacement to ensure compliance?
Materials used for combustible cladding replacement include non-combustible options like:
- Aluminium Composite Panels (ACP) with fire-resistant cores.
- Solid aluminium or steel panels.
- Fibre cement boards and stone-based cladding.
These materials are rigorously tested to ensure compliance with Australian safety standards.
- What risks are associated with not replacing combustible cladding?
Failing to replace combustible cladding can result in:
- Fire hazards and increased risk of fire spread.
- Legal liabilities for building owners due to non-compliance.
- Increased insurance premiums or policy cancellations.
- Endangerment of occupants and property damage in case of combustible cladding fire.
- How do you ensure compliance during the combustible cladding replacement process?
Compliance is ensured through:
- Detailed inspections by fire and façade engineers.
- Use of certified materials with documented test reports during combustible cladding replacement.
- Performance-based design briefs and fire engineering reports.
- Final site inspections and certifications from qualified professionals.
- What is involved in the pre-construction phase of cladding replacement?
The pre-construction phase includes:
- Initial documentation reviews and site inspections.
- Assessments of façade systems (thermal, waterproofing, and substructure).
- Design workshops and material specification to ensure compliance.
This phase sets the foundation for a safe and successful combustible cladding replacement process.
- What types of inspections are conducted during a cladding replacement project?
Inspections include:
- Pre-construction inspections: Assess the existing combustible cladding and substructures.
- During construction: Inspect material delivery, anchor points, and installation quality.
- Post-construction inspections: Verify compliance and provide final reports.
- How does replacing combustible cladding improve building value and safety?
Replacing combustible cladding enhances a building by:
- Eliminating combustible cladding fire hazards, improving safety for occupants.
- Ensuring compliance with updated building regulations and standards.
- Enhancing the building’s value and reducing insurance costs.
- Demonstrating a commitment to occupant safety and modernisation.
- What certifications are required after completing combustible cladding replacement?
Post-replacement certifications include:
- Final compliance certifications issued by fire engineers.
- Façade engineer design certificates.
- Site inspection reports verifying all fire and safety measures are met.
These certifications confirm that the combustible cladding replacement process has been completed successfully.
Thank you for your visit, and welcome to the construction home